Sheet metal brakes serve the purpose of bending thin metal sheets for various projects like house siding, eaves, and air conditioning ductwork. This guide will assist in building a simple sheet metal brake for DIY enthusiasts.
Steps
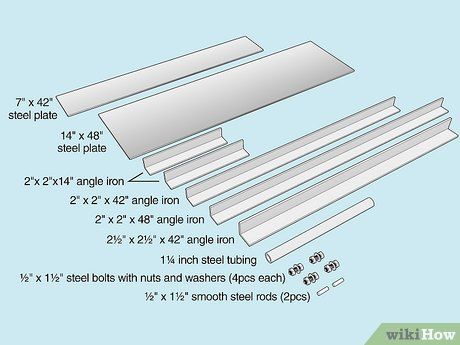
Selecting sturdy materials is crucial for your project. Utilizing a 1⁄4 inch (0.6 cm) steel plate with bracing allows bending of 14 gauge galvanized steel sheet metal up to 3 feet (0.9 m). Below are the materials required for this brake:
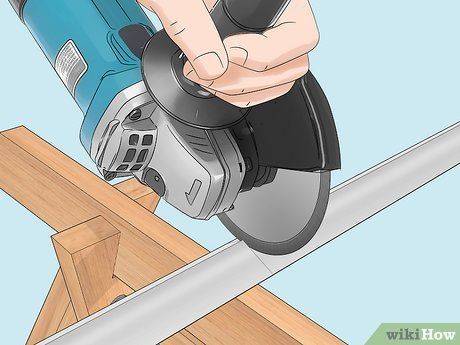
Cutting the angle iron and steel plate into specified sizes is essential. Ensure edges are square and straight. Place the 14' wide plate on sawhorses or a workbench for fitting the remaining pieces.
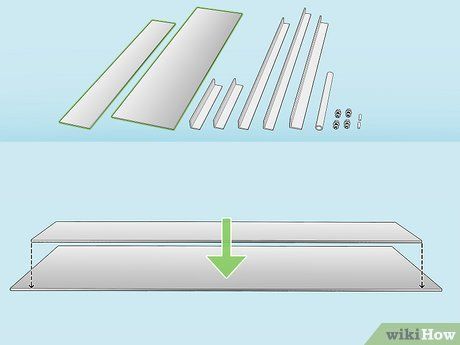
Position the 7'X42' piece atop the 14' piece, aligning the front edges and leaving equal space on both ends. Secure them with clamps if desired to prevent shifting during subsequent steps.
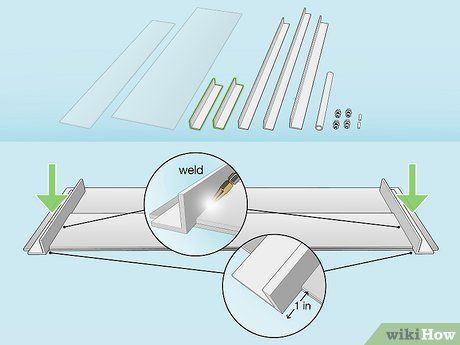
Place one of the 14' angles on each end of the 7' wide (top) plate, ensuring it extends about 1 inch (2.5 cm) beyond the front edge, and weld them to the plate. These angles will serve as clamping hinges when assembling the brake.
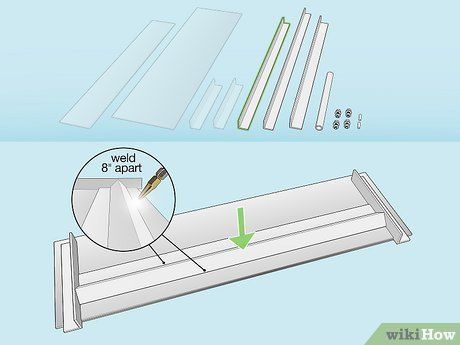
Center the 42' piece of 2' angle iron on the 7' wide (top) plate, aligning it between the end angles and weld it in place with the angle facing up. Apply at least one-inch welds on each edge, spaced 8 inches (20.3 cm) apart. This reinforces the plate for clamping metal in the brake.
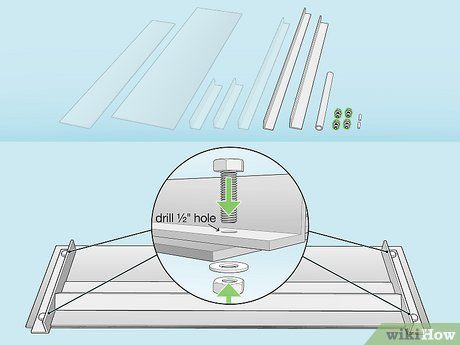
Drill 1/2-inch holes in the flats of the two 14-inch (35.6 cm) angles, one near the front edge and one near the back edge of the 14' wide plate. While the bolt placement isn't crucial, aligning them with each other and on each end enhances the appearance. Loosely bolt each angle to the plate using 1/2-inch bolts.
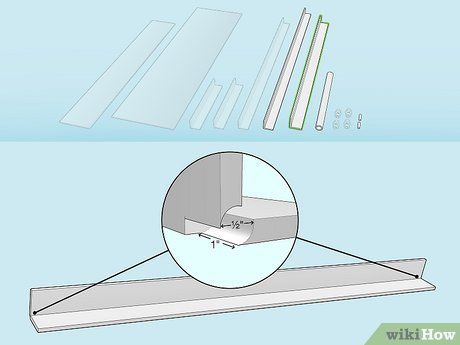
Notch the angle points at each end of the 2 1/2-inch (1.3 cm) angle, making a notch 1/2 inch (1.3 cm) wide and 1 inch (2.5 cm) deep to accommodate the hinge pins. The exact positioning will depend on the brake's alignment, but centering the 1/2-inch rods in the angle's corner should suffice.
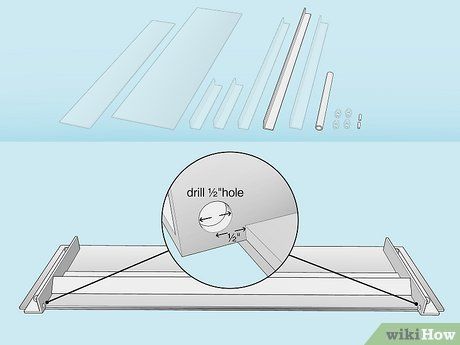
Drill 1/2-inch (1.3 cm) holes 1/2 inch (1.3 cm) beyond the front edges of the 7' plate through the 14'X2' angles where they extend over the front of the plate just above the bottom flange of the angle iron. These holes will accommodate the hinge pins.
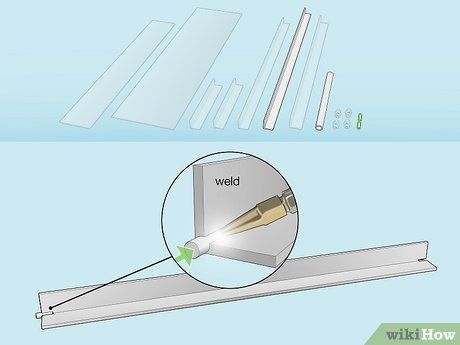
Weld one of the smooth 1/2 rods into a notch cut into the 2 1/2' angles, ensuring it extends at least 3/4' beyond the end of the angle. Maintain straight alignment with the corner of the angle iron for unrestricted swiveling when installed.
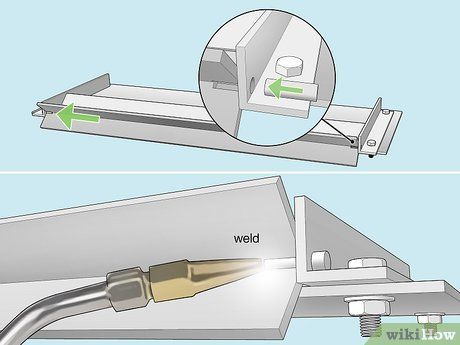
Insert the welded pin (1/2 smooth rod) into the previously drilled socket, then align the other notch with the socket on the opposite end to fit the second pin into place. Weld this pin to the angle iron.
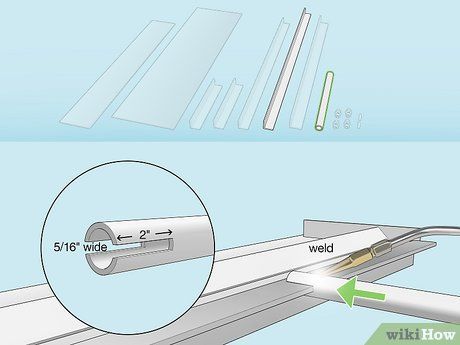
Notch the steel pipe 5/16' wide by 2' deep to slide over the top angle, forming a handle to operate the newly installed braking angle. Center it on the angle and weld it securely into position.
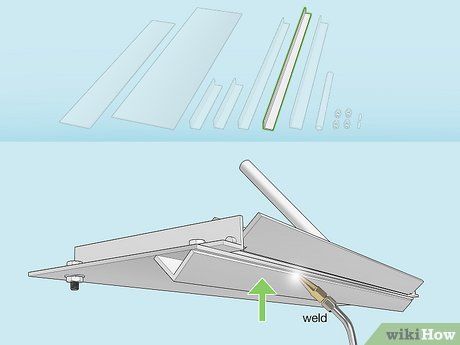
Flip the brake over (it will be heavy) and position the 1 1/2' X 48' angle near the front edge of the 14' wideX48' steel plate. Weld it in the same manner as the upper stiffener.
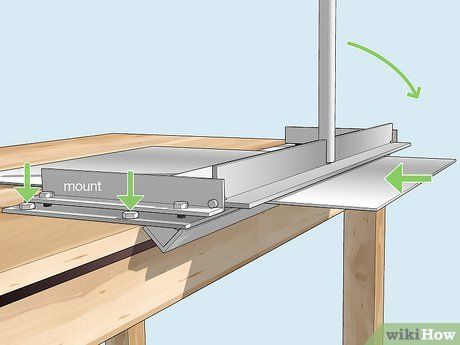
Mount the brake on sawhorses or your workbench with a few inches hanging over to allow the brake and slide a piece of sheet metal between the 7' and 14' plates. Snug the bolts down to clamp it, and pull the pipe handle towards you to bend the metal.
Tips
- Opt for heavier metal stock to create a stronger brake capable of bending heavier sheet metal or longer widths.
- Test fit all the pieces by tack welding them before completing the project, allowing for adjustments if necessary.
- Consider mounting this machine on pipe stands anchored to the floor or in the ground for long-term use.
Warnings
- If assembled correctly, this brake should facilitate clean corners, but mastering its use will require practice. Start with scrap metal to test and fit before using it on your finished pieces.
- Practice safe techniques when cutting metal, welding, and drilling.
Equipment Needed
- Metal cutting tools
- Drill
- Welder
- Materials listed in the steps above