Mechanics depend on torque wrenches to deliver precise and dependable torque measurements, enabling them to exert the correct amount of force on vehicle nuts and bolts. However, it's essential to regularly calibrate torque wrenches to ensure accurate readings. While seeking professional calibration is advisable, you can maintain the accuracy of your torque wrench quite effectively by calibrating it at home.
Steps
Evaluating the Calibration of the Torque Wrench
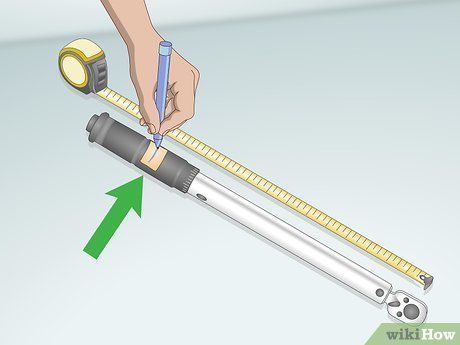
Measuring from the square drive to the handle: The square drive refers to the end of the torque wrench where a socket is attached. For simplicity, use whole inches instead of fractions. Mark the measured point on the handle and record the distance on a piece of paper for future reference.
- Set the paper aside in a secure location until needed.
- Considering that most torque wrenches are 24 inches (61 cm) in length, this measurement will be used in subsequent steps.
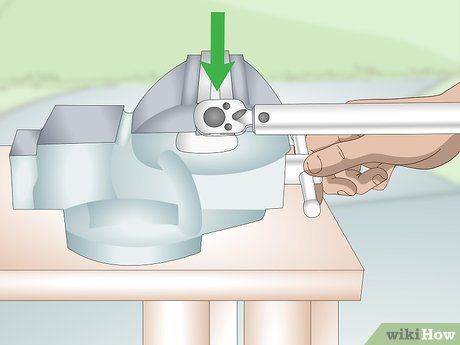
Secure the square drive in the vice. Position your bench vice to accommodate the square drive of the torque wrench, allowing the handle to extend away from the surface. Insert the square drive into the vice and tighten it securely.
- Ensure not to over-tighten the vice to prevent damaging the square drive.
- Verify that only the square drive is clamped, allowing the wrench to move under applied weight.

Determine the appropriate setting based on weight. Use the formula: handle distance multiplied by weight divided by 12. To find the correct setting, multiply the distance measured in step 2 by the weight you will apply (20 pounds). This results in 480 inch-pounds (24 inches multiplied by 20 pounds), equivalent to 40 foot-pounds (480 inch-pounds divided by 12).
- If using metric units, convert the weight to Newtons by multiplying kilograms by 9.807. For instance, 9.07 kg x 9.807 = 88.94949 Newtons. Then, multiply Newtons by the length in meters: 88.94949 Newtons x 0.6096 meters = 54.2 Newton meters.
- To convert foot-pounds to Newton meters, multiply by 1.35582. Therefore, 40 foot-pounds equals 54.2 Newton meters.
- Ensure accuracy by using the correct distance and weight values. Different wrench sizes or weights will yield different figures.
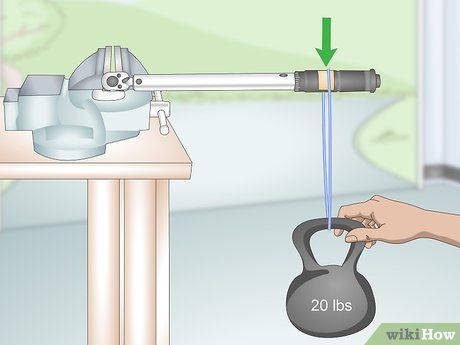
Suspend weights from the wrench handle. Attach a rope to the weight, creating a loop to hang from the torque wrench handle where the mark was made in step 1. Ensure the rope length prevents the weight from touching the ground once hung.
- Avoid securing the weight tightly to the wrench; simply let it hang.
- Ensure no obstructions support the weight as it hangs.
Rectifying Torque Wrench Calibration
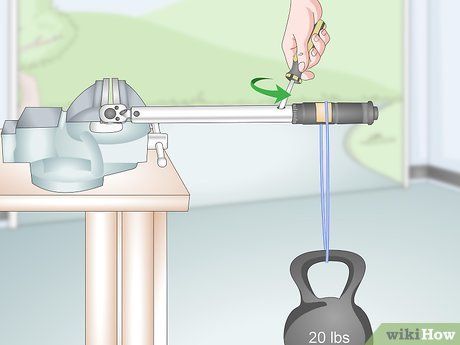
Adjust the torque wrench using the weight. Typically, you can adjust spring tension in a torque wrench by turning a screw midway up the handle using a screwdriver. Hang the 20 lb (9.1 kg) weight from the torque wrench at the initial mark and check for a click. If none occurs, tighten the spring by turning the screw clockwise. Lift and lower the weight to test.
- Repeat until the torque wrench clicks using the specified weight.
- Ensure to lift the weight off the wrench and lower it to test for clicking each time.
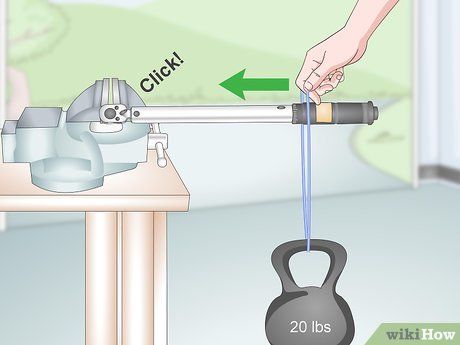
Adjust the weight position upward upon hearing a click. Listen for the torque wrench click as you hang the weight from the marked spot on the handle. If a click is heard, lift the weight off and move it further up the handle towards the head of the wrench.
- Continue this process until the click ceases.
- Remember to lift and set down the weight each time. Avoid sliding it along the handle.
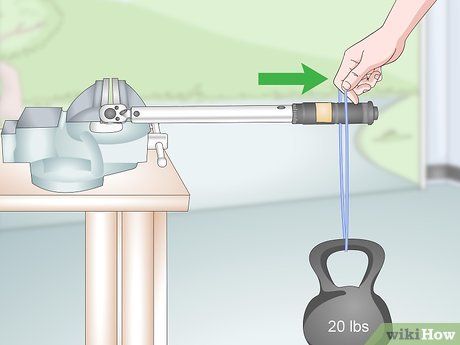
Move the weight downward if no click is heard. In case the torque wrench does not click upon placing the weight, shift the weight down the handle until a click is heard.
- Start with small increments of about an inch.
- You may need to move the weight up and down the handle multiple times to locate the point where the click initiates.
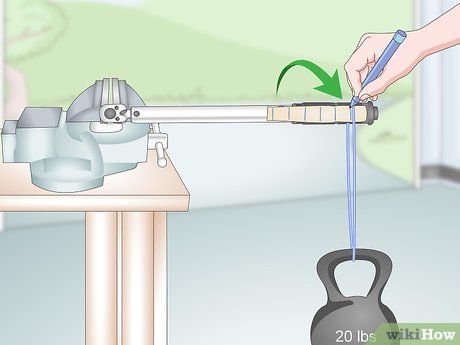
Identify the transition point. Once you discern where the handle switches from clicking to silence, mark it precisely on the wrench using a pen. Ensure accuracy by making several attempts to pinpoint the transition point by adjusting the weight position.
- This marked area on the handle indicates the transition point.
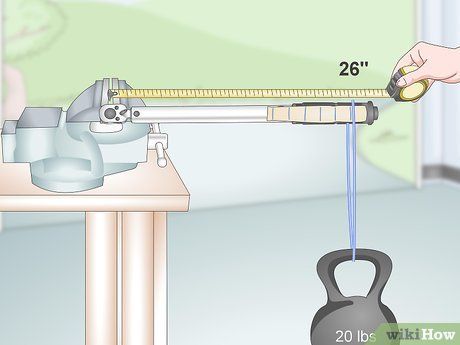
Determine the distance from the square drive to the transition point. Utilize a measuring tape to measure the distance from the square drive to the marked transition point identified using the weight. Record this measurement on a piece of paper. This example uses a measurement of 26 inches (66 cm), but yours may differ.
- Be cautious not to confuse this measurement with the one recorded in step 2.
- Consider repeating the process of identifying the transition point to ensure accuracy in your measurement.
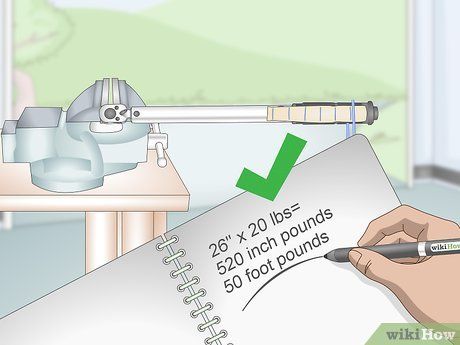
Calculate the applied torque. For example, if the torque wrench transitioned at 26 inches with a 20-pound weight, multiply by 20 pounds to determine the applied torque: 26 inches times 20 pounds equals 520 inch-pounds, or 43.33 foot-pounds (520 divided by 12 inches).
- The formula remains the same: measurement length multiplied by weight, divided by 12.
- If using metric units, convert the weight to Newtons (kg x 9.807), then multiply the result by the length in meters: 9.07 kg x 9.807 = 88.95 Newtons. 88.95 Newtons x 0.6604 meters = 58.74 Newton meters.
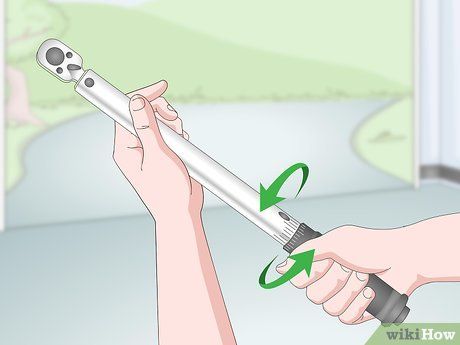
Compensate for the identified variance. If adjusting the torque wrench isn't feasible, you can still achieve relatively accurate results by modifying the settings on the wrench to counteract the variance. Divide your initial measurement by the transition point (for instance, 24 divided by 26 equals 0.923). Whenever you use the torque wrench, multiply the desired torque by this factor.
- Multiplying your intended torque by the variance factor will yield the appropriate setting for your specific torque wrench.
- This approach allows continued usage, although the wrench still requires calibration.
Sustaining the Updated Calibration
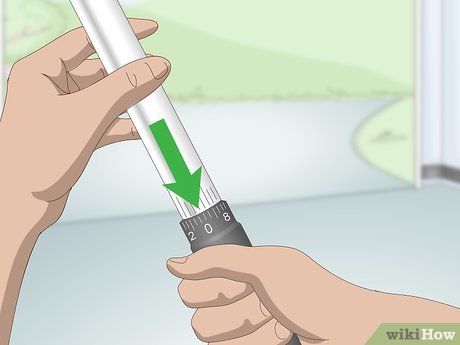
Reset the scale to zero after each use. Although torque wrenches require regular calibration, you can extend the intervals between calibrations by resetting the torque wrench setting to zero after each use.
- Failure to return the wrench to zero can lead to calibration drift due to strain on the internal spring.
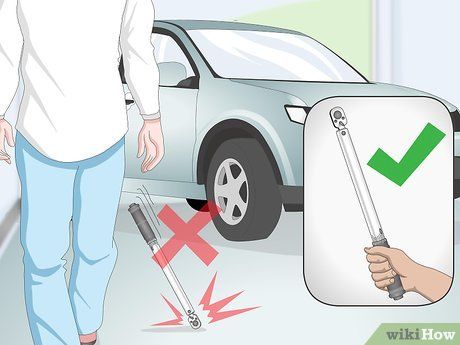
Maintain a firm grip on the torque wrench. Dropping the torque wrench onto a hard surface can immediately impact its calibration. Always place the wrench down carefully to prevent drops, and avoid using it as a hammer or lever.
- Rough handling can promptly alter calibration.
- Torque wrenches may even break upon impact from a fall.
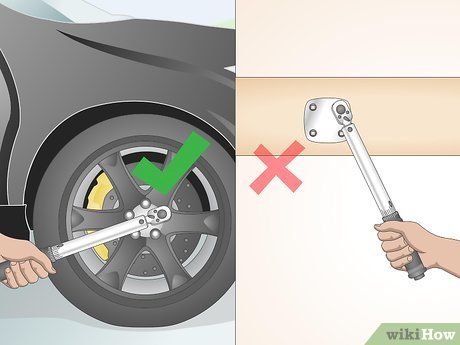
Use the torque wrench only for suitable tasks. Despite resembling a breaker bar, a torque wrench should only be employed when precise torque specifications are required. Misusing the wrench for other purposes can compromise its calibration.
- Substituting a torque wrench for a breaker bar or different tool can damage its calibration or the wrench itself.
- Consider the torque wrench as a specialized tool rather than a universal one.
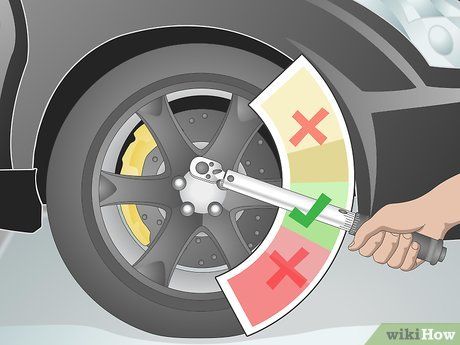
Adhere to the torque wrench's specified torque range. Going beyond the designated torque limits of a wrench can lead to damage or affect its calibration. Most torque wrenches clearly indicate their upper and lower torque tolerances. Avoid tasks requiring more or less torque than your wrench can handle.
- Exceeding the maximum torque limit may result in wrench breakage.
- A damaged torque wrench may lose its calibration stability.
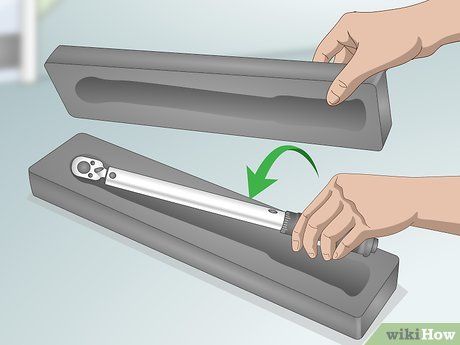
Store your torque wrench in its designated case and separately from other tools. Due to their sensitivity to impacts and environmental changes, it's advisable to store your torque wrench in its protective case and away from frequently used tools.
- Keep the torque wrench stored low to minimize potential damage from falls.
- Store the torque wrench in a controlled environment to prevent adverse effects from temperature or humidity fluctuations.
Helpful Suggestions
-
Ensure the weight used is precisely 20 pounds (9.07 kilograms).
-
If unsure about calibrating the tool yourself, consider seeking professional assistance. Professional shops have the necessary equipment and expertise for accurate calibration.
-
Always lift the weight off the wrench handle when locating and confirming the click point to ensure its accuracy.
Essential Equipment
- Bench clamp or vice
- An object weighing 20 pounds (9.07 kilograms)
- Thin rope or string
- Measuring tape
- Marker
- Calculator or paper and pencil (optional)