Air compressors empower the use of pneumatic tools, streamlining DIY projects. These machines are also perfect for beginners, as putting one together is as straightforward as connecting the hose and power cord. Keep an eye on the pressure gauges to ensure the air pressure in the hose stays below the level specified for your power tool. Remember to adjust the pressure when switching tools and release the drain valve after usage. Following these steps each time ensures safety and efficiency in your work.
Steps
Preparing the Compressor
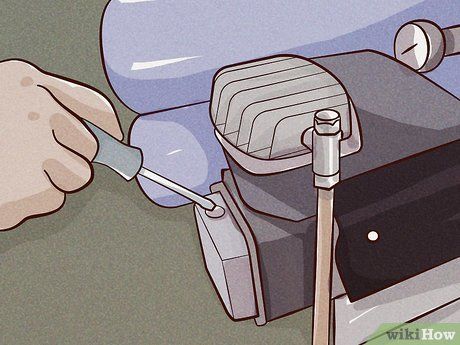
Inspect the pump oil level if your compressor isn’t oil-free. Older and larger compressors typically use oil. Locate the dipstick near the bottom of one end of the compressor. Pull it out and ensure the oil level is around ⅔ of the way up the dipstick. If it's low, add some compressor oil to the tank.
- Compressor oil is available at most home improvement, hardware, and auto parts stores.
- If you're unsure about your compressor type, consult the owner's manual. Most small compressors nowadays are oil-free, which is why you might not see an oil tank or dipstick.
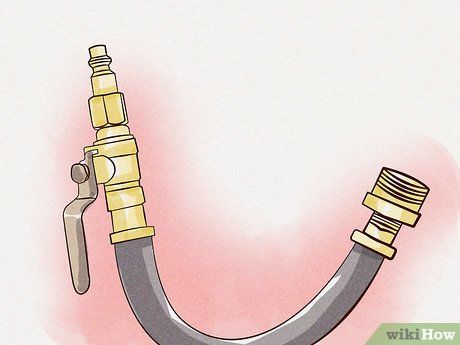
Connect the hose to the regulator valve. Position the compressor on a level surface. Locate the regulator valve, typically situated near the smaller pressure gauge on one end of the compressor. It resembles a round, copper-colored metal plug with a large hole in the middle. Insert the pointed end of the hose into the valve to attach it securely.
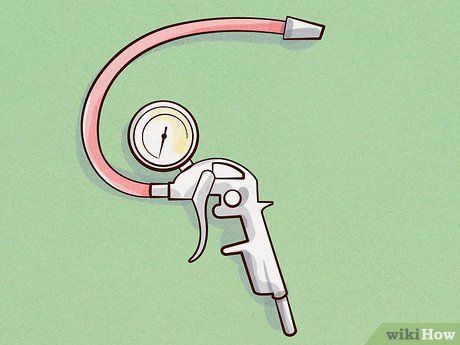
Attach your power tool to the hose. Hold the hose in one hand and the power tool in the other. Insert the tool's plug into the free end of the hose and twist them together until the tool is securely locked in place. A properly attached tool won't come loose during use.
- If you're inflating a tire, press the coupler onto the tire's valve.
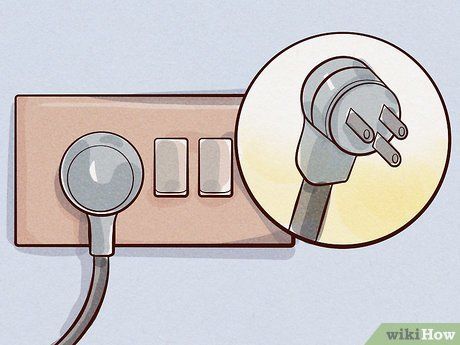
Plug the compressor into a grounded 3-prong outlet. Ensure the compressor's power switch is turned off before plugging it in. If you can't reach a working outlet, avoid using extension cords. Instead, use another air hose and connect it to the first one.
- To connect two hoses, insert the plug end of one hose into the receiving end of the other. It's similar to attaching a power tool to the hose.
- Avoid using extension cords as they may cause the compressor to overheat.
Using the Compressor
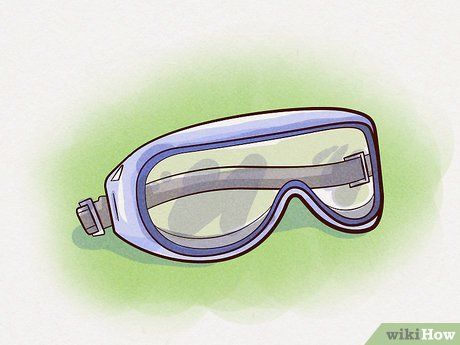
Wear safety goggles and closed-toed shoes. It's crucial to wear proper safety gear when operating power tools. Use polycarbonate goggles to protect your eyes and wear sturdy shoes or boots to safeguard your toes from any falling tools. Don all safety equipment before operating the compressor.
- Considering the noise from tanks and tools, wearing ear muffs is also advisable.
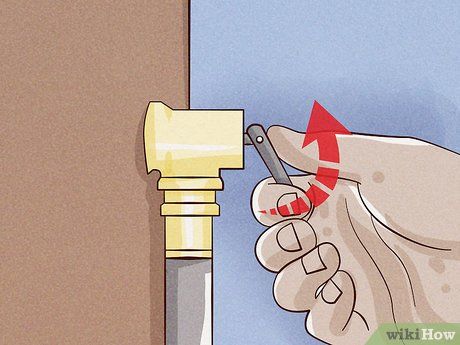
Test the safety valve by pulling on it. Locate the copper-colored plug near the hose line. It should be securely in place on the compressor and may have a ring for easier pulling. Pull it towards you to release the valve and listen for any hissing sound of air escaping. Push the valve back in before starting the compressor.
- If you hear air hissing out, the valve is working. Otherwise, if you can pull and secure the valve without hearing air escape, it should be fine.
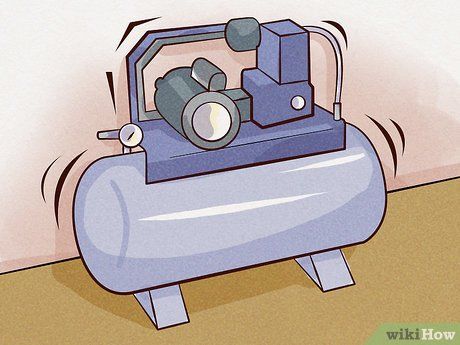
Switch on the compressor and wait for the tank to pressurize. Flip the electrical switch on the tank to activate it. The machine will come to life with a buzzing sound. Keep an eye on the larger pressure gauge on the tank's side. Wait until the needle stops moving, indicating that the air inside has reached maximum pressure.
- The smaller gauge near the hose displays the air pressure in the hose. It will remain unchanged for now, which is normal.
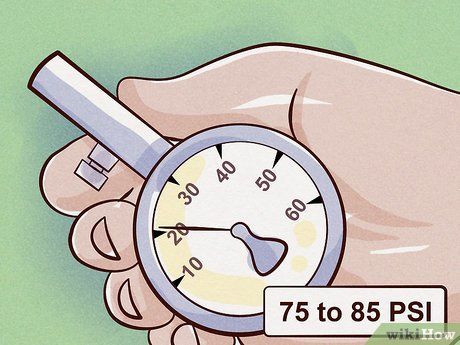
Determine the pressure requirement for your tool. Typically, this information is printed on the tool itself. Look for a sticker or markings on the tool's underside, near the handle. If you can't find it there, consult the owner's manual for guidance.
- For instance, the tool's specifications may indicate a maximum PSI of 90. To ensure safety, maintain hose pressure between 75 and 85 PSI.
- Since each tool has a different rating, you'll need to adjust the pressure whenever you switch tools.
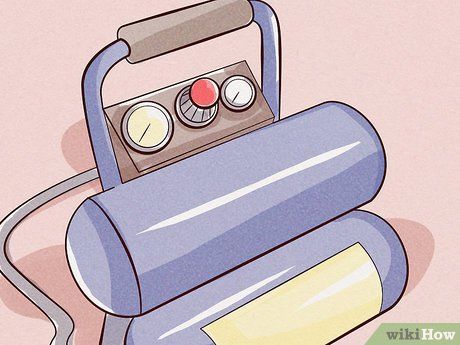
Set the pressure regulator knob to match the tool's PSI. The pressure regulator knob is typically located on the hose. Turn it counterclockwise to increase the airflow into the hose. Monitor the smaller pressure gauge on the hose until it indicates the required pressure level.
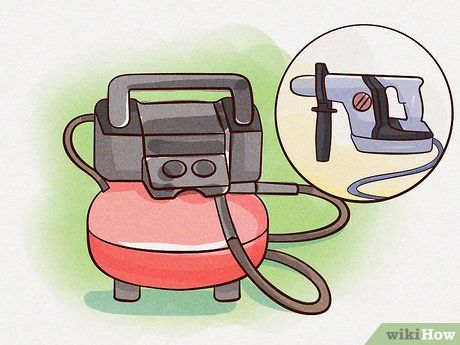
Use the power tool while there's air in the tank. Once the hose has pressurized air, your tool is ready for use. Each time you use the tool, the tank pressure will decrease and automatically begin refilling. You won't need to make adjustments until you switch to a different tool.
- If your power tool suddenly stops working, check the pressure gauge. This can happen with smaller tanks that refill slowly. Wait a moment for the pressure to rebuild.
Turning Off and Maintaining the Compressor
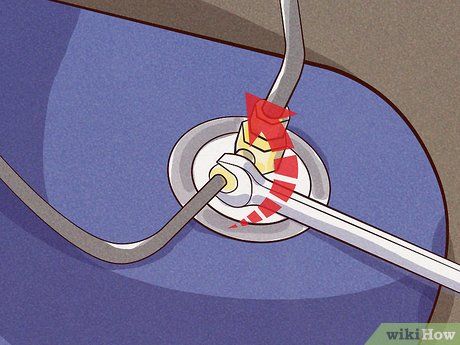
Release condensation by opening the air tank drain valve. Locate the valve on the underside of the air tank. Turn the valve counterclockwise to allow pressurized air to blow out any accumulated moisture. Secure the valve by twisting it clockwise until the air flow stops.
- If you can't turn the valve by hand, try using pliers.
- To ensure your compressor's functionality, drain condensation after each use.
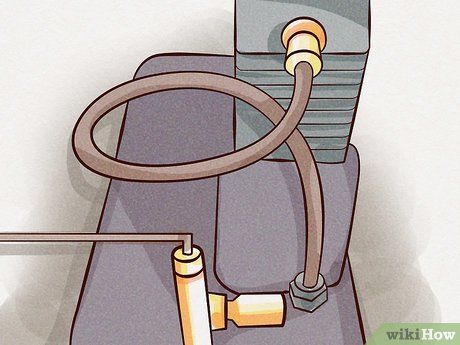
Turn off the compressor to release pressure. Keep the hose in place until the compressor is switched off. Begin by turning the pressure regulator knob near the hose to close off the air supply. Then, power off the compressor and wait for the pressure to dissipate. Use the pressure relief valve to expedite the draining process.
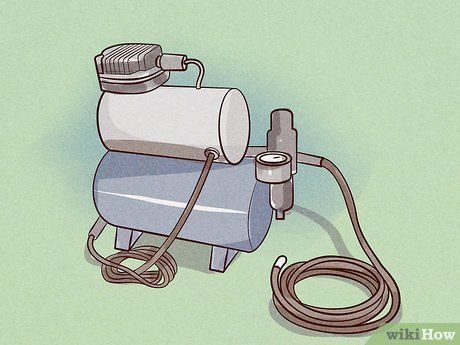
Detach the hose and store the air compressor. Unplug the compressor from the wall outlet, then remove the hose. Without pressure in the tank, the hose should slide out easily. Store both the compressor and hose in a dry, temperature-controlled area such as a closet.
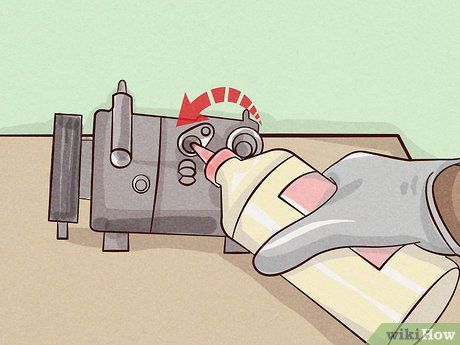
Change the oil annually for oil-filled compressors. Clean oil is crucial for the proper functioning of any machine. To do this, use a socket wrench to remove the plugs from the oil tank. Have a container ready to catch the old oil. Then, use a funnel to pour in fresh compressor oil.
- Refer to your owner’s manual for detailed instructions on accessing the oil tank and replacing the oil.
Helpful Tips
-
Opt for compressors with higher ratings for quicker filling, reducing downtime between tool uses.
-
While most small compressors are oil-free and wear out faster than oil-filled ones, they eliminate the need for oil checks or changes.
-
Consider larger compressors for their increased air capacity, making them ideal for handling bigger tools such as paint sprayers.
Important Warnings
Avoid using extension cords as they can cause compressor overheating and pose a fire risk. Instead, use additional hoses for extended reach when necessary.
Prior to usage, always check the pressure guidelines specified for each tool. Never exceed the recommended pressure limit to prevent damage or accidents.
Essential Tools You'll Need
-
Compressor oil for oil-filled compressors
-
Socket wrench for oil-filled compressors
-
Bucket to catch old oil
-
1 or more air hoses
-
Air compressor
-
Compatible power tools
-
3-pronged outlet
-
Safety goggles
-
Close-toed shoes
-
Pliers
The content is developed by the Mytour team with the aim of customer care and solely to inspire travel experiences. We do not take responsibility for or provide advice for other purposes.
If you find this article inappropriate or containing errors, please contact us via email at [email protected]