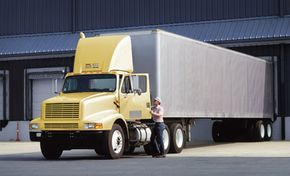
Picture this: It's your first week on the job as a dockhand at a shabby trucking company. The place is buzzing with activity as everyone rushes to load the final pallet of cargo onto a massive tractor-trailer headed cross-country. Suddenly, a foreman tells you to move one of the trucks so another driver can back into the loading dock. Assuming you’re capable of driving one, the foreman carries on, but you freeze – because you’re not.
Eager to impress the higher-ups and ignoring the fact that you lack a truck driver’s license, you jump into the driver’s seat, close the door, and turn the key. Just before the diesel engine roars to life, you’re hit by an ear-piercing alarm and a flashing dashboard light. You start the engine, but the sound and light won’t stop.
Having driven a stick shift before, you think you know what you're doing. Despite the chaos around you, you press the clutch, grab what you assume is the low gear, and slowly release the clutch. Instead of moving forward as you expect, there's a loud bang, the engine stalls, and you’re nearly thrown out of the cab.
You try restarting the engine, thinking you might have put the truck in the wrong gear, and select what you believe is the correct one. Yet, the buzzer and flashing light continue to wreak havoc in the cab. Maybe the emergency brake is still engaged. Unable to find any familiar brake handle or lever like you’d see in a car, you decide to release the clutch and give it another attempt.
To your embarrassment, the same issue occurs again. Out of the corner of your eye, you spot that same foreman yelling at you from the loading dock. Frustrated, you leap out of the cab, raise your hands in confusion, and watch as the annoyed supervisor rushes toward you.
Welcome to the world of air brakes. In this article, you’ll discover how air brakes and their components function, how to maintain an air-brake system, and why you couldn’t move that truck. Now, let’s dive into how George Westinghouse played a part in getting you into this mess.
George Westinghouse and the History of Air Brakes
Air is everywhere, but hydraulic fluid isn’t. Trains, buses, and tractor-trailers use air-brake systems to avoid depending on hydraulic fluid in car braking systems, which can run out if there’s a leak. These vehicles carry heavy loads of passengers or cargo, making safety a top priority. A high-speed locomotive relying on hydraulic brakes would turn into a lethal steel projectile if its brake system failed due to a fluid leak.
Before air brakes, trains relied on a basic braking system that required a brakeman in each car to manually apply a handbrake when signaled by the train's engineer or director. This labor-intensive and inefficient method was eventually replaced by direct air-brake systems, which used an air compressor to send air through a brake pipe into air tanks on each car. When the engineer activated the brakes, air would flow into the pipe, engaging the brakes.
In 1869, an engineer named George Westinghouse recognized the need for improved safety in the emerging railroad industry and invented the first triple-valve air-brake system for use on railcars. Westinghouse’s system worked differently from direct air-brake systems. The triple-valve system, as the name suggests, performed three key functions. Let’s break down those functions.
- Charging: The system must be pressurized with air before the brakes will release. When at rest, the brakes stay engaged. Once the system reaches the required operating pressure, the brakes are released and ready for use.
- Applying: When the brakes are applied, air pressure drops. As the air decreases, the valve lets air flow back into the reservoir tanks, causing the brakes to engage.
- Releasing: After the brakes are applied and air escapes post-braking, the increased pressure helps release the brakes.
Instead of using force or directed air like hydraulic fluid in cars, the triple-valve system fills a supply tank and relies on air pressure to release the brakes. Essentially, the brakes stay fully engaged until air is pumped throughout the system. It's a clever design—if the system loses all air, the brakes automatically engage to stop the train. Now think about this when you’re driving down the highway and you press the brake pedal: If your car’s brake fluid leaked out, your brakes wouldn’t function.
The triple-valve system is the foundation of today’s air-brake systems found in trains, buses, and tractor-trailers. Let’s shift focus now and explore how air brakes function in road vehicles in the next section.
On June 27, 1988, a commuter train collided with a stationary train at the Gare de Lyon station in Paris, France, resulting in 56 deaths and 32 injuries [source: AP, National Geographic]. The tragedy was caused by a series of errors that drastically reduced the train's braking power. After a passenger accidentally engaged the emergency brake while exiting, the driver shut a brake valve, mistakenly thinking the system had an air lock. When he released the air, the train began rolling freely, but the other cars with a charged system lacked sufficient stopping power. In a moment of panic, the driver failed to activate the electric emergency braking system, leading to the crash with a parked train. If not for the brave driver in the stationary train who stayed to assist in passenger evacuation, the death toll would have been far higher [source: AP, National Geographic].
Understanding How Brakes Work
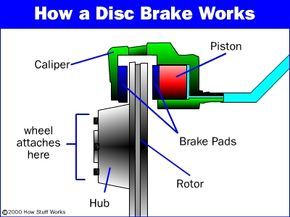
Before diving into air brakes used in road vehicles, let’s first examine how the brakes in your car function. Anyone who has driven a car knows that when you press the brake pedal, the car slows down and eventually comes to a stop. But how can we possibly stop a 3,000-pound (1,361-kg) car moving at high speeds with just our foot on a pedal?
To begin, let’s explore the various types of brake systems and their components. Every moving vehicle, including trains, trucks, buses, and cars, uses one of two systems. Hydraulic brakes, found in light-duty trucks and passenger cars, rely on hydraulic fluid or oil to operate. Air brakes, which we’ll explore in detail in the next section, use air to activate their braking mechanism. Let’s compare the two systems.
In a hydraulic brake system, fluid is stored in a reservoir called the master cylinder. When you press the brake pedal, the fluid is pushed through hoses or lines into pistons mounted on each wheel. These pistons then either press against brake shoes, which expand and create friction inside a brake drum, or they push against a brake pad that clamps onto a brake rotor. Below are the key components of a hydraulic disc brake system.
- Brake reservoir: Holds hydraulic brake fluid
- Master cylinder: The component that pumps fluid from the reservoir into brake lines that extend throughout the vehicle
- Brake lines: Flexible rubber or steel-braided hoses that connect the master cylinder to each brake caliper
- Brake caliper: A metal housing attached to a fixed point on the brake rotor, containing a piston and brake pads
- Brake piston: A cylindrical rod that extends outward and presses against the brake pad when hydraulic fluid flows from the master cylinder
- Brake pad: A metal-backed pad with a semi-metallic coating that clamps onto the steel rotor to stop the wheel's rotation
- Brake rotor: A steel disc mounted to each wheel and hub, which the brake pads press against to halt the wheel’s movement
[source: Brakes]
Here’s a look at how some of the components work together in a disc brake system.
Before disc brakes, vehicles relied on drum brakes. The basic mechanics were similar, but drum brakes used brake shoes inside a drum mounted on the hub, whereas disc brakes use a rotor. Disc brakes provide better stopping power, as they cool more efficiently and offer a larger surface area for grip. Additionally, they vent brake dust, which forms as the brake pads wear down, much more effectively than drum brakes. For more details on the mechanics of disc and drum brakes, check out How Disc Brakes Work and How Drum Brakes Work.
Now that we've covered the basics of brakes in cars and trains, let’s shift our focus to large trucks and buses.
Components of Air Brakes in Trucks and Buses
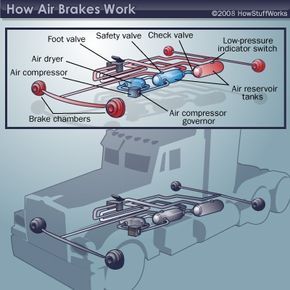
Foundation brakes, which are the most common air-brake systems used in trucks and buses, operate in a manner similar to air brakes in rail cars. Utilizing the triple-valve principle, air accumulates in the brake lines, releasing the brakes. Nearly all road vehicles with air brakes are equipped with a graduated release system, where a minor increase in air pressure leads to a proportional release of the brakes.
Here are the components exclusive to a foundation air-brake system in trucks and buses:
- Air compressor: Compresses air into storage tanks for use in the braking system
- Air compressor governor: Regulates the activation and deactivation of the air compressor, ensuring the air tanks maintain a consistent pressure
- Air reservoir tanks: Store compressed air that powers the braking system
- Drain valves: Release valves located on the air tanks, used to expel air when the vehicle is idle
- Foot valve (brake pedal): Releases air from the reservoir tanks when pressed
- Brake chambers: Cylindrical containers housing a slack adjuster, which moves a diaphragm or cam mechanism to activate the brakes
- Push rod: A steel rod that connects the brake chamber to the slack adjuster, activating or releasing the brakes when pressed or extended
- Slack adjusters: A lever that connects the push rod to the brake s-cam, adjusting the distance between the brake shoes
- Brake S-cam: An S-shaped cam that forces the brake shoes apart, applying pressure to the brake drum
- Brake shoe: A steel component with a friction lining that presses against the brake drum to stop the wheels
- Return spring: A spring attached to each brake shoe that returns the shoe to its open position when it’s not being engaged by the s-cam or diaphragm
When the vehicle is idle (foot off the brake and air system fully charged), air pressure holds the diaphragm or keeps the s-cam in the closed position, resulting in the brakes being disengaged. Upon pressing the brake pedal, the air pressure drops, causing the s-cam to rotate and push the brake shoes against the drum. The air compressor then refills the reservoir tanks, and when you release the pedal, air pressure returns to its original level, releasing the brakes.
Emergency air brakes serve as an additional safety feature to the standard air-brake system and are activated by pulling a button located on the dash (near the light button we discussed earlier). Before operating a vehicle with air brakes, you must engage the emergency brake by pressing the button to fill the system with air. The emergency brake will stay disengaged as long as the system remains pressurized. However, if there's a leak causing a loss of pressure, the emergency brake will engage automatically. Additionally, many heavy trucks are equipped with an exhaust brake, which helps slow the vehicle down but relies on the engine, not the air-brake system.
We’ve covered how air brakes function. Next, let’s explore how proper maintenance can prevent brake failure in the upcoming section.
Have you ever noticed the funny squeaking and hissing sounds coming from trucks and buses? The squeak is air escaping after the brakes are applied, while the ppssss sound comes from the bypass safety valves ensuring the air pressure remains within the proper range. One of the main benefits of air-brake systems is their ability to use air to operate, meaning the compressor continually switches on and off to refill the air reservoirs. When the compressor generates too much air pressure, the valves open to release it, causing that distinctive hissing sound.
Air Brakes: Preventative Maintenance
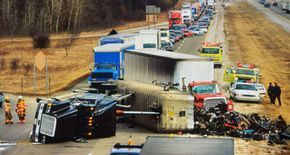
Each state in the U.S. has its own set of regulations for operating vehicles equipped with air brakes. Obtaining a commercial driver’s license requires passing rigorous tests, and maintaining such a vehicle involves several essential steps. Before hitting the road, here are a few important actions to consider:
- Ensure that the minimum operating pressure for a vehicle’s air-brake system is at least 85 psi (pounds per square inch) for buses and 100 psi for trucks.
- Verify that it takes no longer than two minutes for the air pressure to rise from 85 psi to 100 psi at 600 to 900 rpm. This is known as the air pressure buildup rate.
- Check that the correct cut-out governor pressure for the air compressor is between 120 psi and 135 psi. The cut-in pressure should be 20 psi to 25 psi lower than the cut-out pressure.
It’s also important to check for water in the air-brake system, which results from condensed air. Water can be harmful to air-brake lines, especially in colder environments where it can freeze and block air flow to the brake mechanism, causing the wheels to lock. Many modern systems include automatic drain valves in each air tank to mitigate this issue.
Air couplers can present issues as well. Worn-out rubber seals may lead to air leaks. Although the compressor can manage a small leak, overworking it can cause failure. As we’ve learned, a loss of air pressure isn’t always detrimental, but it will leave you stranded. For truck drivers, finding yourself stuck on a mountain pass is definitely not part of the plan.
Brake sensitivity, a common feature of air-brake systems, can be a hazard, especially for drivers who are still gaining experience. These systems are specifically designed for vehicles that carry heavy loads. Have you ever wondered why you see multiple skid marks on the expressway? That's often due to light or empty trailers locking up their rear wheels. One of the biggest fears for truck drivers is jackknifing, which occurs when the back of the trailer swings up next to the cab. Trucks traveling through rain and snow are particularly vulnerable to jackknifing if too much braking force is applied.
Most modern air-braked vehicles are equipped with a dual system, meaning that they have two independent brake systems in case one fails. Tractor-trailers, for example, now come with Anti-lock brakes (ABS), which function in a similar way to the ABS systems found in passenger vehicles.
In principle, air brakes are both efficient and dependable. However, don't expect to find them in your car anytime soon. Air brake systems require significant space and maintenance, making them impractical for passenger vehicles. Just take a look at a Peterbilt truck cruising down the highway. Have you noticed the large tanks behind the fuel tanks? Now, imagine trying to fit those under the hood of a Honda Civic.
On April 25, 1996, a 1988 Mack cement truck collided with a Subaru sedan in Plymouth Meeting, Pa. As the truck approached an intersection at the bottom of a downhill ramp, its brakes failed, causing the truck to crash into the intersection and hit the Subaru, resulting in the death of the sedan’s driver. The National Transportation Safety Board (NTSB) later investigated the crash and identified several issues with the truck, including reversed brake lines and a secondary system failure. These problems left the truck with only about 17 to 21 percent of its total braking capacity. Tragically, the driver was unaware of the brake failure. This unfortunate incident was a result of poor maintenance and could have been easily prevented. [source: NTSB]
Air Brake Diagram
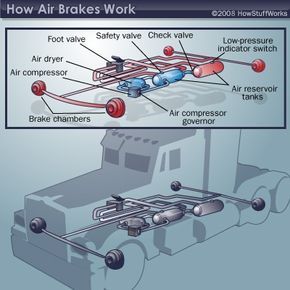
Let's now combine the individual parts to see how air brakes function as a complete system. This diagram offers both a detailed close-up and an illustration showing the placement of the brakes within your vehicle.