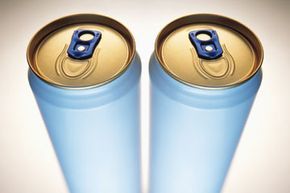
With just a few soda cans and some easy-to-find materials, you can recreate one of the first practical engines ever developed. Despite its small size, the Coke can Stirling engine taps into our mechanical heritage, quietly spinning a flywheel, turning fan blades, or even producing a bit of power.
Its straightforward design evokes a sense of nostalgia for a different era. Whether seen as a working model, an intriguing conversation starter, or a kinetic artwork, building a soda can Stirling engine is an enjoyable way to connect with the past.
The Stirling engine was conceived by Robert Stirling in 1816. His vision was to use air to drive the engine, offering an alternative to the steam power technology that was emerging at the time.
What distinguished Stirling's engine from others was its use of an "economizer," later known as a regenerator, which improved fuel efficiency. Between 1816 and 1843, Stirling and his brother James fine-tuned the engine's design and performance. By the mid-19th century, their engines were powering major industries like foundries. However, most hot air engines, including Stirling's, were better suited for low-power tasks. While Stirling aimed to create a safer alternative to the hazardous steam engines of the time, his engine's power limitations eventually hindered its widespread use in larger industries.
The first thing to understand about a Stirling engine is how its components fit together and how they function.
Materials Needed to Build a Coke Can Stirling Engine
Remove Stirling's regenerator, and you're left with a simple hot air engine. The principle behind a hot air engine is straightforward: air acts as the "working fluid." A heat source, such as a tea light candle in most soda can Stirling engines, warms the air, causing it to expand. Once the air cools, it contracts. This expansion and contraction create a thermodynamic cycle. By using this cycle to move a piston, you harness mechanical work. Attach a crankshaft to the piston and add a flywheel, and you’ve got the fundamentals of an engine.
Building a Stirling engine offers more than just technical knowledge—it’s a hands-on lesson in DIY engineering. It’s also a lot of fun, allowing you to get creative with materials that many might consider scrap. Watching it run takes the experience to a whole new level.
Sounds easy, right? It is, but there's still quite a bit of work ahead before the engine is fully assembled. You'll need additional parts, materials, and a solid understanding of how they all come together to get your engine running smoothly.
Here's the list of materials you'll need:
- Three (3) soda cans
- One (1) balloon
- Two (2) spoke nipples
- Four (4) 5A electrical terminal blocks
- Steel wire wool
-
- Steel wire
- Copper wire
- Dowel rod
- Electrical wire
- Fishing wire
- Three (3) compact discs
- Can opener
- Utility knife
- Super glue [source: ScrapToPower.com]
Now, let’s explore the individual components you’ll be assembling, how they function, what role they play, and how everything comes together to make your engine work.
While Robert Stirling wasn’t the first to attempt an air-powered engine, he was the first to create a commercially successful version. His engine design, introduced in 1818, was used to power a water pump at a quarry.
Getting Ready to Build a Coke Can Stirling Engine
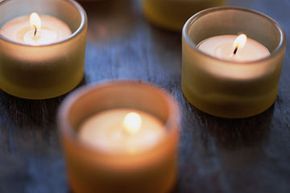
"You have to think like a watchmaker," says Jim Larsen, a seasoned Stirling engine builder, author, and educator. "Pay attention to the details. Focusing on the small things gives you a better chance of success."
The key parts of a Stirling engine are relatively basic and straightforward. Although we’re focusing on a soda can engine, Stirling engines have been made from various materials, ranging from paint cans to oil drums. Larsen shared that during a Thanksgiving visit with his in-laws, he built a Stirling engine using an assortment of hardware store materials, including pots and pans.
Aluminum soda cans are ideal for engine construction—they offer pre-formed shapes that are easy to work with and, naturally, inexpensive. While they might not be sturdy enough for heavy-duty use, they are perfectly adequate for withstanding the minimal power produced by most Stirling engine designs.
The pressure chamber is the container that holds the air, or working fluid, in a sealed system. It is within this chamber that the air undergoes heating and cooling throughout the thermodynamic cycle. While pressure and air leaks can be problematic for many engines, the pressure chamber actually requires a small, controlled leak. Without this leak, the chamber would simply act as a barometer, responding only to fluctuations in the barometric pressure of the surrounding air.
Larsen mentioned that many Stirling engine builders prefer to use helium instead of air as the working fluid in the pressure chamber, as helium performs more efficiently during the thermodynamic cycle.
The drive mechanism harnesses the expansion and contraction of air inside the pressure chamber to turn a crankshaft. This mechanism can either be mounted on the side of the engine or integrated directly into the engine's structure.
For Larsen, the crankshaft is the most crucial component of the engine, influencing every part of the system, from timing and displacer movement to flywheel speed and overall balance. "This is the part that deserves your full attention to get it just right," said Larsen.
Putting Together a Coke Can Stirling Engine
The flywheel is not just a sign that the engine is operational. It functions as a sort of energy reservoir. A properly balanced flywheel captures the energy produced during the power stroke of the motor and stores it. When it's time to move the displacer, the flywheel releases its stored energy to overcome friction and other opposing forces. Without an efficient flywheel, the displacer would simply rise to the top of the chamber and remain there.
Larsen emphasized that a well-balanced flywheel is crucial for optimal performance. If the wheel is unbalanced, the engine has to exert extra effort to move it. "You don't want the engine to work harder than necessary," he stated.
In a hot air engine, the displacer is responsible for shifting the air inside the pressure chamber. Remember, the engine relies on the thermodynamic cycle, where air is alternately heated and cooled, causing it to expand and contract. If the chamber were heated without a component to displace the air, the air would expand but fail to contract.
With the heat source positioned at the bottom, the hot air engine also utilizes cooling at the top, often using ice or cold water, to cool the air. As the air heats up, it expands, pushing the displacer toward the top of the pressure chamber. When the air reaches the top and cools, it contracts, driving the displacer back down. This entire process is aided by the drive mechanism, crankshaft, and flywheel.
The displacer is typically a rolled-up piece of steel wool with a light wire running through its center. Remember when Larsen advised thinking like a watchmaker? This is one of those moments. The displacer must slide freely within the pressure chamber while filling most of it. It needs to allow air to flow smoothly, while still restricting some of the flow. The goal is to minimize friction and maximize efficiency. This principle is key throughout the engine's construction.
The heat box is essentially the platform on which the engine sits, with the heat source placed beneath it to power the engine.
It may seem like a lot of effort for minimal output, but there’s something deeply satisfying about completing the engine, fine-tuning it to make it work, and watching it run on its own. For Larsen, this passion began over five decades ago, and for you, it could spark in just a few days.
To see a soda can Stirling engine in action, check out this video along with other similar videos online.