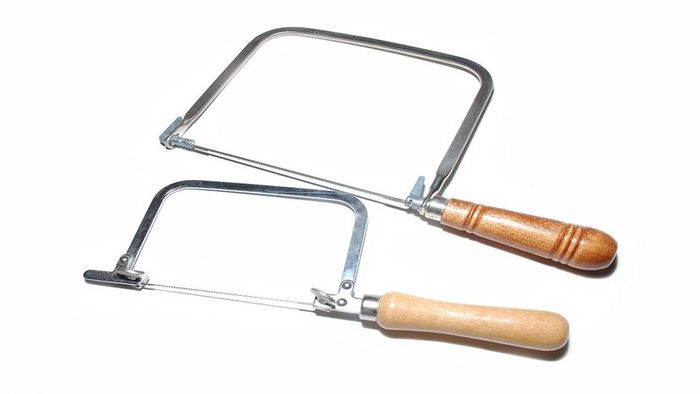
Important Points to Remember
- Coping saws are perfect for making precise, detailed cuts through wood, plastic, or metal. They feature a U-shaped frame and a delicate, tensioned blade that can be adjusted to various angles relative to the frame.
- These saws are especially useful for intricate tasks, such as fitting joints in crown molding, thanks to their ability to make turning cuts. The blade's teeth density (12 to 15 teeth per inch) varies depending on the cutting requirements.
- The handle, typically crafted from hardwood or plastic, offers better control during cutting. Some versions also feature a mechanism to adjust blade tension, boosting the tool's adaptability for a wide range of projects.
The coping saw derives its name from a carpentry technique called the cope, where two pieces of wood trim are joined on the inner wall of a structure. For a secure fit and a seamless look, the wood must be cut in a curved shape first.
In 1887, Christopher Morrow patented the “coping saw,” featuring a tensioned blade. By 1900, the tool was being sold in catalogs and saw widespread use.
What Exactly Is a Coping Saw?
Coping saws are handheld saws with a unique U-shape, ideal for making curved cuts in thinner materials, commonly used around the house and workshop.
A coping saw employs a thin steel or tungsten blade stretched within a metal frame to perform curved cuts on materials like wood, plastic, or metal, depending on the selected blade. Its design closely resembles a hacksaw, though it has a larger gap, referred to as "the throat," between the blade and the frame. The U-shaped frame features swiveling clips (spigots) at both ends to secure the blade. A handle made of hardwood or plastic allows the user to rotate the blade while cutting. Many coping saw handles include a tension adjustment feature, allowing users to twist and set the blade's tension. Some saws also allow the blade’s angle to be adjusted relative to the frame. These features make the coping saw ideal for precise curved cuts, such as those needed when crafting joints for crown molding.
Most coping saw blades feature approximately 12 to 15 teeth per inch, although coarser and finer blades can be found for specialized tasks. Blade lengths are generally available in either 6 3/8 inches (16 centimeters) or 6 1/2 inches (16.51 centimeters). The throat width typically ranges between 4 and 6 inches (10.16 to 15.24 centimeters). Like most hand saws, you can easily find one for purchase at any local hardware store.
Other handy handsaws include the crosscut saw, ripsaw, backsaw, keyhole saw, and hacksaw. Additionally, electric jigsaws can be used for some tasks typically handled by a coping saw.
However, our focus here is on the coping saw.
How to Safely Operate a Coping Saw
To install a blade, position the frame's front edge on a bench with the handle pointing upwards. Attach one end of the blade to the spigot farthest from the handle. Then, press down on the handle to compress the frame, allowing you to attach the other end of the blade. Release the tension and adjust the spigot as needed. Before you begin cutting, ensure the blade is securely tensioned within the frame to prevent it from loosening. Be cautious not to overtighten, as this can cause the blade to snap. If cutting into the center of a material, you may need to remove the blade, pass it through a pilot hole in your material, and then reattach it to the saw frame.
To safely operate the coping saw, securely hold the material in a vise or with clamps. Using a carpentry pencil to draw the intended design on the material will provide a visual guide for accurate cutting. Position the saw's central teeth along the cut line and push the saw away from your body in short strokes to begin. Keep following the line, adjusting the handle and frame as needed to stay on track. For wood and soft materials, you may wish to sand the cut afterward to achieve a smooth, flush edge.
For safety, keep your hands, fingers, and other objects away from the sharp teeth of the saw. Never apply more pressure than you could with your bare hands. As with any bladed tool, wear long sleeves, padded work gloves, and safety glasses to protect yourself from the blade or debris. Long hair should be tied back and kept clear of the cutting area to avoid any interference during the process.
How to Care for Your Coping Saw
Like most hand tools, a coping saw should be stored in a dry place to prevent rust. If rust appears on the frame, particularly around the tensioners, it's advisable to replace the saw. Also, dull or corroded blades should be swapped out before use.
After several cuts, the saw blade will probably lose its sharpness, making the work more challenging. Most coping saw blades are designed to be easily removed and replaced by the user. Replacement blades are available at most hardware stores. Be sure to select the correct blade based on the number of teeth per inch. For cutting wood, a coarse blade with around 15 teeth per inch should suffice, while harder materials require finer blades and a bit more effort.
Different Types of Coping Saw Blades
When operating a coping saw, selecting the right blade is as crucial as executing the cut itself. Replacement blades come in various types, designed specifically for the materials they are intended to cut.
- Wood Cutting Blade — The most common option. These blades are made of steel and typically range from 15 to 18 teeth per inch, offering a good balance of speed and precision. Fewer teeth allow for faster cutting, while a finer blade offers more control but cuts more slowly.
- Plastic Cutting Blade — Featuring helical teeth that spiral like a drill bit, this blade is perfect for cutting through soft materials like plastic or clay without damaging their edges. Minimal pressure should be applied when using this blade.
- Metal Cutting Blade — Crafted from high-carbon steel, these blades are designed to cut through thin sheet metal. For cutting thicker metal, however, a power saw is often required for safety.
- Tile Cutting Blade — Equipped with a tough tungsten carbide wire, this blade is made to cut through hard materials such as ceramics.