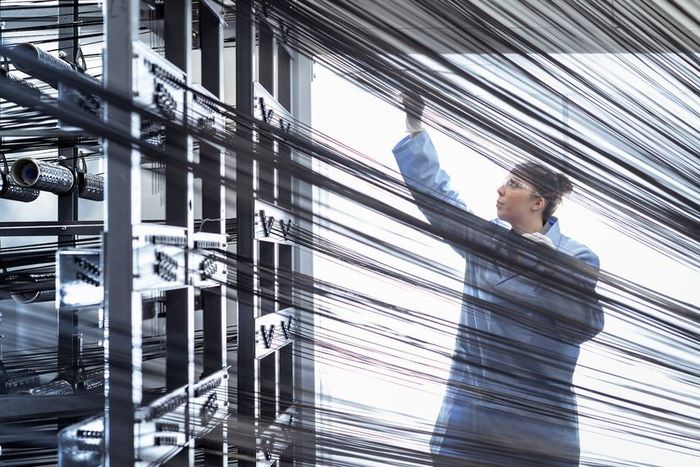
As the Industrial Revolution progressed, a series of revolutionary inventions shaped the course of history. Constant innovations and refinements led to increased efficiency and output, with many of these devices becoming fully automated thanks to their brilliant inventors.
The power loom stands out as one of the most influential inventions of the early Industrial Revolution, sparking a dramatic shift in the textile industry and paving the way for the creation of cotton mills and expansive textile factories.
What Is a Power Loom?
The power loom, a pivotal innovation of the Industrial Revolution, was a mechanical device created to automate the weaving process. Its successful implementation was crucial in transforming the textile industry by minimizing reliance on manual labor and drastically changing fabric production methods.
Power looms represented a monumental change from traditional cottage industries (which employed manual looms using the flying shuttle) to large-scale factory-based production, increasing efficiency, output, and market reach.
How Does a Power Loom Work?
The power loom functioned based on automation and mechanical energy. It incorporated a series of complex mechanisms that eliminated the need for a specially trained operator to manually weave the fabric.
The first power loom, introduced in the late 18th century, adapted British technology from English textile mills and incorporated several essential components:
- The warp, the longitudinal yarn set, is kept under tension on a beam.
- The weft, the crosswise yarn, is inserted through the warp using a shuttle or other mechanisms.
- The loom is driven by mechanical devices and power sources such as belts, pulleys, and gears, which control the motion of both the warp and weft threads.
Unlike the earlier handloom, which relied on human power to weave fabric, the power loom used a system of gears, pulleys, and belts powered by a steam engine or other energy sources.
The loom's automated function greatly accelerated the weaving process and boosted efficiency. Successful power looms could replace up to thirty manually operated looms.
Designers of the Power Loom
Ongoing advancements and improvements played a crucial role in the development and widespread implementation of power looms throughout the textile industry.
Edmund Cartwright
One of the key inventors linked to the creation of the power loom is Edmund Cartwright, an English clergyman and inventor. In 1785, Cartwright patented his design for the power loom. Although he is credited with the initial invention, it was Richard Arkwright who made substantial refinements to its design.
Richard Arkwright
Arkwright revolutionized the factory system by integrating the power loom with his earlier invention, the water frame, resulting in a more efficient and cohesive textile production system. His groundbreaking use of water-powered spinning machines alongside power looms paved the way for the factory system and the mechanization of the textile industry.
James H. Northrop
It's worth mentioning that many inventors and engineers continued refining power loom technology over time. For instance, in the early 20th century, James H. Northrop introduced the Northrop loom, which enhanced the efficiency and automation of power looms by incorporating a mechanism for the continuous filling of the weft thread.
Why Were Power Looms Important?
Power looms were critically important to the textile industry for a variety of reasons. Most importantly, they dramatically increased the speed of textile production. The shift from manual labor to power looms allowed factories to manufacture fabrics at a far faster rate. With power looms, a single machine could accomplish what would have previously required multiple weavers working on handlooms.
Power looms were also instrumental in the growth of the American textile industry. Francis Cabot Lowell, an American entrepreneur, saw the potential of power looms and adapted British technology to create the first fully integrated textile factory in the early 19th century.
This factory system, which integrated spinning and weaving processes under one roof, became the model for future textile mills. The introduction of power looms ultimately set the stage for the textile industry to achieve higher standards and scale up production.
There was also a significant impact on the socioeconomic landscape. Operating power looms was not only faster but also required fewer workers. Cottage industries, once reliant on the manual labor of skilled weavers, began to collaborate with factories.
This caused a major shift in employment patterns, as automation began to replace the need for skilled handweavers, leading to a growing demand for factory workers.
Power Looms and the Modern World
Power looms continue to be in use today, though their designs and technologies have evolved considerably since their early days during the Industrial Revolution. Modern power looms are now sophisticated, computer-controlled machines that offer enhanced efficiency, precision, and automation in textile manufacturing.
Modern weaving machines are designed with advanced programming capabilities that allow them to create intricate patterns, switch designs with ease, and monitor several variables to ensure the production of top-notch fabric. These machines are commonly utilized in large textile manufacturing operations to produce a wide variety of materials, including cotton, wool, silk, synthetic fibers, and blends.
These looms are designed to manage high volumes of production, capable of weaving fabrics with diverse patterns, textures, and widths. The ongoing advancements and widespread use of power looms have empowered textile manufacturers to satisfy the needs of the global market, enabling them to produce fabrics in bulk quantities.