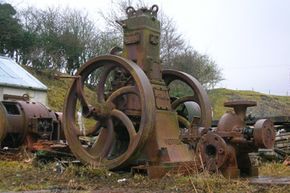
During the era when steam dominated, and gas and diesel engines were still emerging, hot bulb engines were highly popular. These engines could utilize any liquid fuel, operate without a battery ignition—sometimes for extended periods—and were known for their efficiency, simplicity, and durability. For farmers, fishermen, or sawmill operators, where toughness and dependability were crucial, hot bulb engines were the ideal choice.
However, these engines had limitations. They operated within a narrow rpm range, typically between 50 and 300, which restricted their applications. They were most effective as stationary engines, although some tractors employed this technology for slow movement. Starting the engine was challenging, and maintaining its operation required significant effort.
Despite their limitations, hot bulb engines continued to be utilized well into the 1950s and even the 1960s in some remote rural regions. Today, they hold a special place among collectors and stand as a significant milestone in the development of gas engines. Their versatility in running on various fuels could inspire modern engineers to design engines capable of handling a broader range of alternative fuels.
Continue reading to delve deeper into the workings of hot bulb engines.
Making it Go
Hot bulb engines feature the same fundamental parts as most other internal combustion engines. The explosion, or burning of gases, forces a piston inside a cylinder. This piston is linked to a flywheel through a crankshaft and connecting rod, enabling the engine to transform thermal energy (from combustion) into mechanical energy at the flywheel. The flywheel then powers any connected mechanical device.
In contrast to gasoline and diesel engines, combustion in a hot bulb engine occurs in a distinct chamber known as the "hot bulb" or "vaporizer." This bulb typically extends horizontally from the engine's front, close to the cylinder. Most hot bulbs resemble a darning mushroom in shape and contain a metal plate, similar to a saucer, which heats up along with the bulb.
Fuel was introduced into the hot bulb through a nozzle, typically a small metered orifice valve. Upon hitting the heated metal plate, the fuel vaporized, combined with air, and ignited. A narrow passage linked the bulb to the cylinder, allowing the expanding gases to travel through and drive the piston.
Unlike gas engines that rely on electricity to ignite a spark plug and start the crankshaft, hot bulb engines require manual heating. On a mild day, around 60 degrees Fahrenheit (15.6 degrees Celsius), the bulb needs heating for two to five minutes, extending to half an hour in colder conditions or for larger engines. Early methods used a blow torch, later replaced by coils and spark plugs, to generate the initial heat needed to vaporize the fuel.
To start the engine, an operator manually spun the flywheel, the heaviest component of the engine, often weighing hundreds of pounds even in smaller models. This continued until combustion began and the engine started running independently.
Once operational, the heat from combustion maintained the bulb's temperature, allowing the engine to sustain itself. However, in low-load scenarios or cold environments, the bulb required additional heating, either periodically or continuously. Despite their simplicity and reliability, hot bulb engines were known for their quirks and occasional unpredictability, which will be explored further on the next page.
British inventor Herbert Akroyd Stuart conceptualized the hot bulb engine in the late 19th century, with the first prototypes built in 1886. English engine manufacturer Richard Hornsby & Sons adopted the design, launching production in 1891 as the "Hornsby Akroyd Patent Oil Engine," a four-stroke model. In the U.S., German immigrants Meitz and Weiss collaborated with Joseph Day to produce a two-stroke version.
By the early 20th century, these engines had gained widespread popularity, with hundreds of manufacturers producing them. They played a significant role in electricity generation, powering dynamos during this period. Sweden became a major user, particularly for fishing boats, with over 70 manufacturers capturing nearly 80% of the market by 1920.
Care and Feeding of Hot Bulb Engines
A major benefit of hot bulb engines was their versatility in using almost any crude fuel. As long as the fuel could flow through a pipe and combust, these engines could operate efficiently.
This adaptability made engines highly sought after in remote areas near oil pipelines, where unrefined fuel was abundant. While primarily stationary, some antique tractors also utilized hot bulb engines for movement. They excelled in industrial settings, providing affordable and consistent power for small workshops or sawmills. However, their low power-to-size ratio limited their use in larger industrial applications, such as powering mills, as a farm tractor required an engine of about 20 liters to function effectively.
Preston Foster, curator of collections at the Coolspring Power Museum and an expert in antique engine restoration, noted that hot bulb engines were well-suited to their era and environment but had certain limitations.
For example, hot bulb engines struggled with refined fuels like gas or diesel. Foster explained, "They primarily ran on kerosene and other less refined fuels."
Hot bulb engines, particularly the two-stroke models, often faced issues like running in reverse or becoming over-fueled, leading to near-uncontrollable operation before the governor could intervene. Foster noted that the engine parts, crafted during a time when metallurgy and machining were still primitive, were prone to breaking, and sourcing replacements was challenging.
In American-made two-stroke versions, the engine sometimes drew oil from the crankcase for fuel, depriving itself of necessary lubrication.
These limitations, alongside advancements in metallurgy and machining, ultimately led to the decline of hot bulb engines.
Ignition timing in hot bulb engines was unpredictable, necessitating a heavy flywheel. Timing depended largely on engine temperature and load.
Prior to 1910, fuel was injected into the vaporizer early in the intake stroke, causing combustion to fall out of sync with the crankshaft angle. This meant the engine operated smoothly only under specific conditions. Changes in load or speed (optimal between 50 and 300 rpm) affected the bulb's temperature and ignition timing, leading to pre-ignition and missed strokes. Many engines employed a water drip system to cool the vaporizer and mitigate pre-ignition issues.
Post-1910 advancements introduced pressurized fuel injection, pumps, and precise delivery, improving timing and reliability while adding some operational flexibility.
Becoming a Part of History
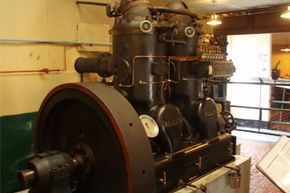
By the early 20th century, advancements in machining resolved most issues with efficient and durable gas and diesel engines. Engineers also addressed challenges related to spark ignition, compression ignition, timing, and engine speed regulation. Additionally, the availability of refined, more efficient fuels increased. These developments contributed to the gradual decline of hot bulb engines.
Examine the power output of hot bulb engines. Despite their size, capable of producing up to 60 horsepower, their compression ratio was modest, around 5 to 1. In contrast, even basic diesel engines achieved a compression ratio of about 15 to 1, delivering greater power and torque in a more compact and practical design.
Hot bulb engines remained in use in Scandinavia until the 1930s and can still occasionally be found in English canal boats. However, today, they are primarily regarded as historical curiosities rather than functional machinery.
"For their era and context, they were an excellent power source," Foster remarked, noting that hot bulb engines couldn't adapt to technological advancements. "They served as a crucial bridge between early engines and modern designs," he added.