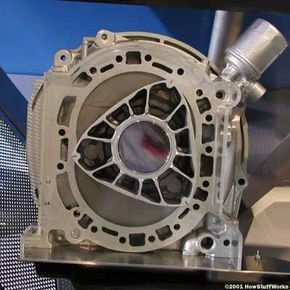
A rotary engine is a type of internal combustion engine, similar to the one in your vehicle, but it operates in a fundamentally different manner compared to traditional piston engines.
In a piston engine, a single cylinder performs four distinct tasks: intake, compression, combustion, and exhaust. A rotary engine, however, accomplishes these same four tasks in separate sections of its housing. Imagine having a dedicated cylinder for each function, with the piston seamlessly transitioning between them.
The rotary engine, initially designed and developed by Dr. Felix Wankel, is often referred to as a Wankel engine or Wankel rotary engine.
This article delves into the workings of a rotary engine, beginning with the fundamental principles that drive its operation.
Principles of a Rotary Engine
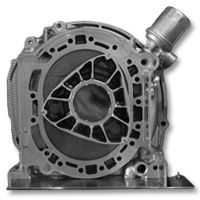
Similar to a piston engine, a rotary engine harnesses the pressure generated from burning a mix of air and fuel. In piston engines, this pressure is confined within cylinders, driving pistons in a back-and-forth motion. The connecting rods and crankshaft then transform this reciprocating motion into rotational energy, which powers the vehicle.
In a rotary engine, combustion pressure is confined within a chamber formed by part of the housing and sealed by one face of the triangular rotor, which replaces traditional pistons.
The rotor moves along a path reminiscent of a Spirograph pattern, ensuring that each of its three tips maintains contact with the housing. This motion creates three distinct gas volumes. As the rotor travels through the chamber, these volumes alternately expand and contract. This process draws in air and fuel, compresses the mixture, generates power through gas expansion, and finally expels the exhaust.
We’ll explore the internal components of a rotary engine shortly, but first, let’s examine a new model car featuring a cutting-edge rotary engine.
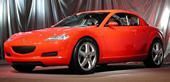
Mazda RX-8
Mazda has been a trailblazer in producing vehicles with rotary engines. The RX-7, launched in 1978, stands out as one of the most successful rotary-powered cars. It was preceded by a range of rotary-engine cars, trucks, and buses, beginning with the 1967 Cosmo Sport. Although the RX-7 was last sold in the United States in 1995, the rotary engine is poised for a revival in the coming years.
The Mazda RX-8, Mazda's latest offering, features an innovative, award-winning rotary engine known as the RENESIS. Recognized as the International Engine of the Year in 2003, this naturally aspirated two-rotor engine delivers approximately 250 horsepower. For additional details, check out Mazda's RX-8 Web site.
The Parts of a Rotary Engine
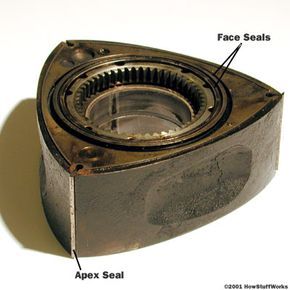
A rotary engine includes an ignition system and a fuel-delivery system similar to those in piston engines. If you’ve never seen the interior of a rotary engine, expect a surprise, as it looks quite different from what you might anticipate.
Rotor
The rotor features three convex faces, each functioning like a piston. Each face contains a pocket, which enhances the engine’s displacement by creating more room for the air-fuel mixture.
Each face of the rotor has a metal blade at its apex, which creates a seal around the outer edge of the combustion chamber. Additionally, metal rings on both sides of the rotor ensure a tight seal against the combustion chamber walls.
Inside the rotor, a set of gear teeth is cut into the center of one side. These teeth interlock with a stationary gear attached to the housing, guiding the rotor’s movement and direction within the engine.
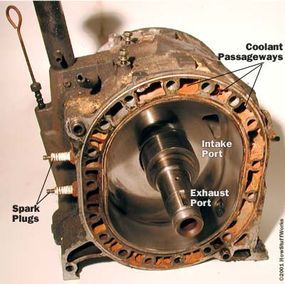
Housing
The housing has an approximately oval shape, technically known as an epitrochoid (you can explore this Java demonstration to understand how this shape is formed). Its design ensures that the rotor’s three tips remain in constant contact with the chamber walls, creating three distinct sealed gas volumes.
The housing is divided into sections, each dedicated to a specific stage of the combustion process. These four sections are:
- Intake
- Compression
- Combustion
- Exhaust
The housing contains both the intake and exhaust ports, which lack valves. The exhaust port is directly linked to the exhaust system, while the intake port connects straight to the throttle.
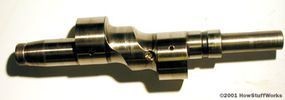
Output Shaft
The output shaft features eccentrically mounted round lobes, positioned off-center from the shaft’s centerline. Each rotor is fitted over one of these lobes. The lobes function similarly to a crankshaft in a piston engine. As the rotor moves along its path within the housing, it exerts force on the lobes. This force, due to the lobes’ eccentric mounting, generates torque in the shaft, causing it to rotate.
Now, let’s explore how these components come together and how they generate power.
Rotary Engine Assembly
A rotary engine is constructed in layers. The two-rotor engine we disassembled consists of five primary layers secured by a series of long bolts. Coolant circulates through channels surrounding all components.
The two outer layers house the seals and bearings for the output shaft. They also enclose the housing sections containing the rotors. The inner surfaces of these layers are highly polished, aiding the rotor seals in performing effectively. Each of these end pieces features an intake port.
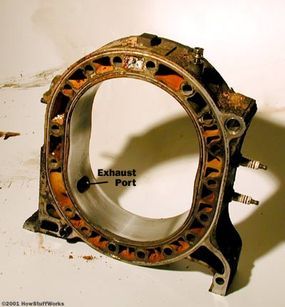
Moving inward, the next layer is the oval-shaped rotor housing, which includes the exhaust ports. This section of the housing is where the rotor is housed.
The central layer features two intake ports, one for each rotor. It also acts as a divider between the two rotors, with its outer surfaces being exceptionally smooth.
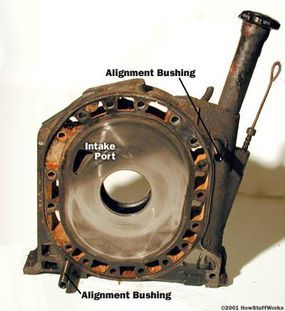
At the core of each rotor is a large internal gear that rotates around a smaller, stationary gear attached to the engine housing. This mechanism dictates the rotor’s orbital path. The rotor also moves along the large circular lobe on the output shaft.
Next, we’ll explore how the engine generates power.
Rotary Engine Power
Rotary engines operate on the four-stroke combustion cycle, identical to that used in four-stroke piston engines. However, the way this cycle is achieved in a rotary engine is entirely unique.
If you observe closely, you’ll notice the offset lobe on the output shaft rotates three times for every full revolution of the rotor.
The core of a rotary engine is the rotor, which serves a similar function to pistons in a piston engine. The rotor is attached to a large circular lobe on the output shaft, which is offset from the shaft’s centerline. This lobe functions like a winch handle, providing the rotor with the necessary leverage to turn the output shaft. As the rotor orbits within the housing, it drives the lobe in tight circles, rotating three times for each single revolution of the rotor.
As the rotor travels through the housing, the three chambers it creates change in size. This variation in size generates a pumping effect. Let’s examine each of the four strokes of the engine by focusing on one face of the rotor.
Intake
The intake phase begins as the rotor’s tip moves past the intake port. When the intake port opens to the chamber, the chamber’s volume is nearly at its smallest. As the rotor progresses, the chamber’s volume increases, pulling in the air-fuel mixture.
Once the rotor’s peak clears the intake port, the chamber is sealed, and the compression phase starts.
Compression
As the rotor continues its path around the housing, the chamber’s volume decreases, compressing the air-fuel mixture. By the time the rotor’s face reaches the spark plugs, the chamber’s volume is nearly at its minimum again, marking the start of combustion.
Combustion
Most rotary engines are equipped with two spark plugs. The elongated combustion chamber requires dual plugs to ensure the flame spreads quickly. When the spark plugs ignite the air-fuel mixture, pressure rapidly increases, driving the rotor to move.
The combustion pressure propels the rotor in a direction that enlarges the chamber’s volume. The expanding gases continue to push the rotor, generating power until the rotor’s peak passes the exhaust port.
Exhaust
Once the rotor’s peak clears the exhaust port, the high-pressure combustion gases escape through the exhaust. As the rotor advances, the chamber begins to shrink, expelling the remaining exhaust. By the time the chamber’s volume nears its minimum, the rotor’s peak passes the intake port, restarting the cycle.
The rotary engine’s unique feature is that each of the rotor’s three faces is continuously engaged in a different phase of the cycle. In one full rotor revolution, three combustion strokes occur. However, since the output shaft rotates three times for every rotor revolution, there is one combustion stroke per output shaft revolution.
Differences and Challenges
Several key characteristics set the rotary engine apart from a conventional piston engine.
Fewer Moving Parts
A rotary engine has significantly fewer moving parts compared to a four-stroke piston engine. A two-rotor rotary engine consists of just three main moving parts: the two rotors and the output shaft. In contrast, even the simplest four-cylinder piston engine contains at least 40 moving parts, such as pistons, connecting rods, camshaft, valves, valve springs, rockers, timing belt, timing gears, and crankshaft.
The reduced number of moving parts in a rotary engine often leads to greater reliability. This is why some aircraft manufacturers, such as the creator of Skycar, favor rotary engines over piston engines.
Smoother
In a rotary engine, all components rotate continuously in one direction, unlike the abrupt directional changes of pistons in traditional engines. Rotary engines are internally balanced with spinning counterweights designed to neutralize vibrations.
Power delivery in a rotary engine is also more consistent. Each combustion event spans 90 degrees of the rotor’s rotation, and since the output shaft turns three times per rotor revolution, combustion lasts through 270 degrees of the output shaft’s rotation. This means a single-rotor engine provides power for three-quarters of each output shaft revolution. In contrast, a single-cylinder piston engine experiences combustion during 180 degrees out of every two revolutions, or just a quarter of each crankshaft revolution.
Slower
Since the rotors rotate at one-third the speed of the output shaft, the primary moving components of the engine operate more slowly than those in a piston engine. This contributes to enhanced reliability.
Challenges
Designing a rotary engine presents several challenges:
- Meeting U.S. emissions regulations is often more challenging (though not impossible) for rotary engines.
- Manufacturing costs tend to be higher, primarily due to the lower production volume compared to piston engines.
- Rotary engines generally consume more fuel than piston engines, as their thermodynamic efficiency is compromised by the elongated combustion chamber shape and lower compression ratio.