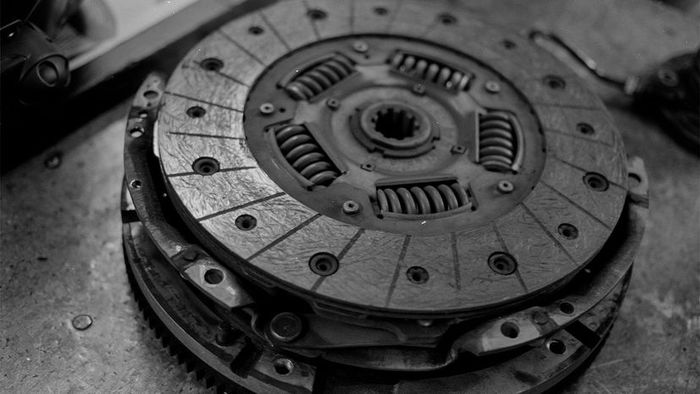
Drivers of manual transmission vehicles might be intrigued to learn that their cars often contain multiple clutches. Interestingly, automatic transmission vehicles also incorporate clutches. Given their prevalence, it’s natural to question how these essential components function in a car.
Clutches are more common than you might think—they’re found in everyday items like cordless drills, chain saws, and even yo-yos. However, today we’ll focus on their role in automobiles. This article will explain the necessity of clutches, how they operate in cars, and reveal some unexpected places where clutches are utilized.
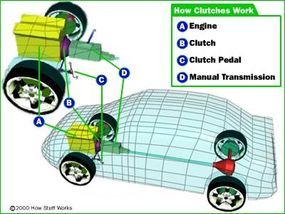
The Reasons For a Clutch System
Clutches play a vital role in machinery with dual rotating shafts, such as automobiles. Typically, one shaft is powered by a motor or pulley, while the other drives an additional component. The clutch serves to link these shafts, enabling them to either synchronize and rotate at identical speeds or disconnect and spin independently.
In vehicles, a clutch is essential because the engine operates continuously, whereas the wheels do not. To bring the car to a halt without stalling the engine, the wheels must be temporarily separated from the engine. The clutch facilitates this by managing the slippage, allowing a smooth connection between the spinning engine and the stationary transmission.
The Role of Friction in Clutches
To grasp how a clutch operates, it’s essential to understand friction, which measures the resistance when one object moves over another. Friction arises from the microscopic peaks and valleys present on all surfaces, even those that appear smooth. The greater these imperfections, the more challenging it becomes to slide the object.
A clutch functions due to the friction generated between the clutch plate and the flywheel. The interaction of these components will be explored in detail in the following section.
Fly Wheels, Clutch Plates, and Friction
In a car’s clutch system, the flywheel is attached to the engine, while the clutch plate is linked to the transmission.
Detailed Breakdown of a Clutch Mechanism
In a manual car, when the clutch pedal is not engaged, springs force the pressure plate against the clutch disc, which then presses against the flywheel. This action locks the engine to the transmission input shaft, ensuring both rotate at the same speed.
The clutch's holding capacity is determined by the friction between the clutch plate and the flywheel, as well as the force exerted by the spring on the pressure plate. This friction operates similarly to the principles explained in the friction section of How Brakes Work, with the key difference being that the spring applies pressure to the clutch plate instead of weight pressing a block onto the ground.
The Process of Engaging and Disengaging a Clutch
Pressing the clutch pedal activates a cable or hydraulic piston, which pushes the release fork. This action presses the release bearing against the diaphragm spring's center, disconnecting the engine from the transmission during gear changes. As the diaphragm spring's center is pushed inward, pins around its edge cause the spring to retract the pressure plate from the clutch disc, thereby releasing the clutch from the engine's rotation.
Notice the springs integrated into the clutch plate. These springs play a crucial role in cushioning the transmission from the abrupt engagement of the clutch. While this design is generally effective, it does come with certain limitations. We’ll explore common clutch issues and additional applications of clutches in the upcoming sections.
Clutch Failure Scenarios
From the 1950s through the 1970s, car clutches typically lasted between 50,000 and 70,000 miles (80,467 and 113,000 kilometers). Modern clutches, when used gently and properly maintained, can exceed 80,000 miles (128,747 kilometers). However, without proper care, clutches may begin to fail as early as 35,000 miles (56,327 kilometers). Trucks that are frequently overloaded or used for towing heavy loads often experience clutch issues, sometimes necessitating multiple clutch discs.
The primary issue with clutches is the wear and tear of the friction linings on the disc. These linings, akin to the friction material on disc brake pads or drum brake shoes, gradually wear down over time. Once the friction material is significantly depleted, the clutch begins to slip and eventually fails to transfer power from the engine to the wheels. Slipping clutches are often termed "wet clutches."
Clutch wear occurs only when the clutch disc and flywheel rotate at different speeds. When they are synchronized and locked together, the friction material remains firmly pressed against the flywheel, spinning in unison. Wear happens exclusively when the clutch disc slips against the flywheel. Therefore, drivers who frequently slip the clutch will experience accelerated clutch wear.
The Clutch Mechanism Gets Stuck
Occasionally, the issue isn’t clutch slippage but clutch sticking. If the clutch fails to release correctly, it will keep rotating the input shaft, leading to gear grinding or even preventing the car from shifting into gear. Common causes of a sticking clutch include:
- Broken or stretched clutch cable: Proper tension is essential for the cable to function effectively.
- Leaky or defective slave and/or master clutch cylinders: Leaks prevent the cylinders from generating the required pressure.
- Air in the hydraulic line: Air disrupts the hydraulic system by occupying space needed for fluid pressure.
- Misadjusted linkage: Incorrect force transmission occurs when the pedal is pressed.
- Mismatched clutch components: Not all aftermarket parts are compatible with your clutch system.
A stiff clutch pedal is another frequent issue. While some force is needed to depress the clutch fully, excessive pressure indicates a problem. Common culprits include sticking or binding in the pedal linkage, cable, cross shaft, or pivot ball. Blockages or worn seals in the hydraulic system can also cause this issue.
Another clutch-related problem is a worn clutch release bearing, also known as a throw-out bearing. This bearing applies pressure to the spinning pressure plate’s fingers to disengage the clutch. A rumbling noise during clutch engagement often signals a problem with the throw-out bearing.
In the following section, we’ll explore various types of clutches and their specific applications.
If no noise is heard during these four steps, the issue likely isn’t related to the clutch. However, if a noise is present at idle and disappears when the clutch is pressed, the problem may lie in the contact area between the release fork and the pivot ball that supports it.
- Start your car, engage the parking brake, and shift into neutral.
- With the car idling, listen for a growling noise without pressing the clutch. If noise is detected, it’s likely a transmission issue. If no noise is heard, move to step three.
- While still in neutral, begin pressing the clutch and listen for noise. A chirping sound as you press indicates a potential issue with the clutch release bearing. If no noise is heard, proceed to step four.
- Press the clutch all the way to the floor. A squealing noise suggests a problem with the pilot bearing or bushing, which links the transmission’s input shaft to the crankshaft.
Types of Clutches
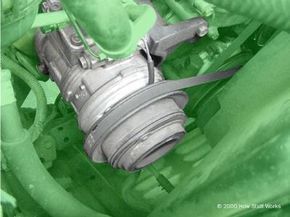
Your car and garage house a variety of clutch types, each serving unique purposes.
Clutch Pedals in Automatic Transmissions
Automatic transmissions utilize multiple clutches to engage and disengage different sets of planetary gears. These gears consist of a central drive gear encircled by orbiting gears. Hydraulic fluid under pressure activates each clutch within the transmission.
When hydraulic pressure decreases, springs release the clutch. Splines, evenly spaced ridges, line the clutch’s interior and exterior to lock into the gears and clutch housing. For more details, refer to How Automatic Transmissions Work.
Electromagnetic Clutch Systems
A car’s air conditioning compressor is equipped with an electromagnetic clutch, enabling the compressor to deactivate even while the engine remains operational. When electrical current passes through the clutch’s magnetic coil, it engages. Conversely, when the current ceases, such as when the air conditioning is turned off, the clutch disengages.
Viscous Clutch with Thermostatic Control
Vehicles with engine-driven cooling fans often feature a thermostatically controlled viscous clutch, where the fluid’s temperature dictates the clutch’s operation. Located at the fan’s hub within the radiator’s airflow, this clutch thickens its fluid as temperatures rise, causing the fan to accelerate and synchronize with the engine’s rotation. When the car is cold, the clutch fluid remains cool, allowing the fan to spin slowly and helping the engine reach its optimal operating temperature more quickly.
Many vehicles incorporate limited slip differentials or viscous couplings, both utilizing clutches to enhance traction. During turns, one wheel spins faster than the others, potentially destabilizing the car. The slip differential compensates by engaging its clutch to slow down the faster wheel and align it with the others. Traction is also improved when driving over water puddles or icy patches, as the clutch prevents wheel spin.
Centrifugal Clutch Systems
Gas-powered tools like chain saws and weed trimmers utilize centrifugal clutches, allowing the chains or strings to halt without needing to shut off the engine. These clutches operate automatically, leveraging centrifugal force. The input connects to the engine’s crankshaft, while the output drives a chain, belt, or shaft.
As the engine’s RPMs rise, weighted arms extend outward, forcing the clutch to engage. Centrifugal clutches are commonly used in lawn mowers, go-karts, mopeds, and mini-bikes. Interestingly, even some yo-yos are designed with centrifugal clutches.
Clutches are indispensable across numerous applications. For further insights into clutches and related topics, explore the links provided below.