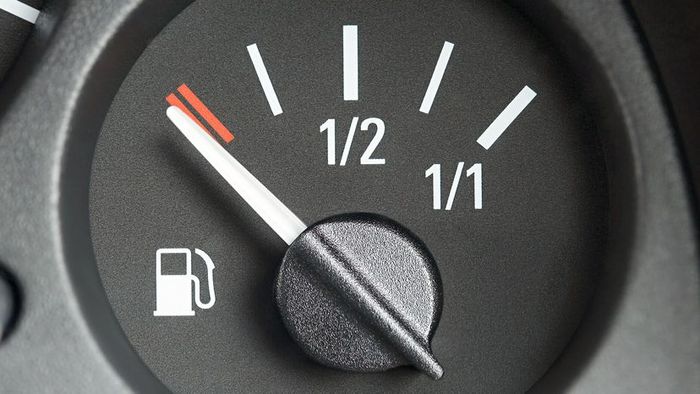
If you share my mindset, you probably aim to maximize every mile from your fuel tank. Gaining an extra 20 miles per fill-up could mean fewer visits to the gas station throughout the year.
The biggest obstacle to maximizing your fuel efficiency is your car's fuel gauge, which often misleads you into thinking you have less fuel than you actually do. These gauges are famously unreliable, indicating empty when there's still plenty of fuel and remaining on full for the first 50 miles.
This article explores the reasons behind the behavior of fuel gauges. A fuel gauge comprises two primary components: the sender, which gauges the fuel level in the tank, and the gauge itself, which communicates this level to the driver. Let's begin by examining how a typical sender operates.
The Sending Unit
The sending unit is housed within the fuel tank of the car. It features a float, typically crafted from foam, attached to a slender metal rod. This rod connects to a variable resistor, an electrical component that restricts the flow of electricity. Increased resistance results in reduced current flow. Inside the fuel tank, the variable resistor includes a strip of resistive material grounded on one side. A wiper linked to the gauge moves along this strip, transmitting current from the gauge to the resistor. When the wiper is near the grounded end, resistance is minimal. Conversely, when it's at the opposite end, resistance is higher due to more resistive material in the current's path.
When the float is at the tank's top, the wiper on the variable resistor is near the grounded (negative) side, resulting in low resistance and a higher current flow back to the fuel gauge. As the fuel level decreases, the float lowers, the wiper shifts, resistance grows, and the current returning to the gauge diminishes.
This design contributes to the inaccuracy of fuel gauges. You might observe that the gauge remains on 'full' for an extended period after refueling. When the tank is full, the float is at its highest position, limited by the rod or the tank's top. This means the float remains submerged and only begins to drop when the fuel level nears the float's bottom. Consequently, the gauge's needle doesn't move until the float starts to descend.
A comparable scenario occurs as the float approaches the tank's base. Typically, the float's movement range doesn't cover the tank's very bottom, allowing it to halt while fuel remains. This explains why, in many vehicles, the needle dips below empty and ceases to move even though there's still gasoline in the tank.
The design of fuel tanks can also lead to inaccuracies. Modern vehicles feature plastic fuel tanks, custom-shaped to occupy compact spaces. These tanks often contour around the car's body or frame, resulting in uneven fuel distribution. Thus, when the float indicates half a tank, the actual fuel volume may differ due to the tank's unique shape.
Let's delve into the mechanics of the gauge.
It might astonish you to discover the actual fuel reserve when the needle points to empty. For precise information, refer to your owner's manual for the fuel tank's capacity. Next time your gauge shows empty, locate the closest gas station and refuel. By subtracting the gallons needed to fill the tank from the manual's stated volume, you'll ascertain the additional distance you can travel even when the gauge indicates empty.
The Gauge
The gauge operates on a straightforward mechanism. Electricity from the sender flows through a resistor, which is either coiled around or positioned close to a bimetallic strip. This strip connects to the gauge's needle via a mechanical linkage, enabling movement.
A bimetallic strip consists of two distinct metals bonded together. These metals expand and contract at varying rates when exposed to heat or cold. The selection of metals ensures their expansion and contraction rates differ, creating the strip's unique properties.
Heating the strip causes one metal to expand less than the other, resulting in a curvature with the more expansive metal on the outer side. This bending motion drives the needle's movement.
When resistance rises, the current through the heating coil decreases, cooling the bimetallic strip. As it cools, the strip straightens, shifting the gauge's indicator from full to empty.
In some modern vehicles, a microprocessor replaces direct current transmission to the gauge. It interprets the resistor's output and relays data to the dashboard, enhancing gauge precision. Let's explore one such system in detail.
Microprocessor-controlled Gauges
Modern vehicles often incorporate a microprocessor that interprets data from the tank's variable resistor and relays it to a dashboard-mounted counterpart. Automakers can fine-tune gauge behavior by aligning float positions with a calibration curve, which maps float location to remaining fuel volume. This adjustment enhances accuracy, particularly in vehicles with irregularly shaped fuel tanks.
Such systems can also activate a fuel light to alert drivers when fuel levels are critically low. Typically, this light illuminates while a few gallons of gas remain, ensuring ample time to refuel.
The microprocessor introduces damping to stabilize needle movement. During turns or uphill drives, fuel sloshes within the tank, causing rapid float position changes. Without damping, the needle would fluctuate excessively. Instead, the system calculates a moving average of recent float positions, resulting in smoother, delayed needle adjustments. This effect is noticeable during refueling, as the needle takes time to reach the full mark after filling the tank.
Although fuel gauges are not perfectly precise, they are designed to err on the side of caution.