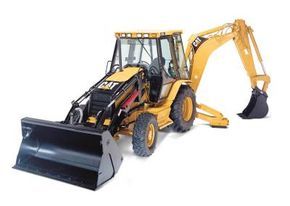
If you asked a group of people about backhoe loaders, many might not recognize the term. However, showing them a picture would instantly clarify. These machines, often referred to simply as backhoes, are ubiquitous on construction sites and are frequently the sole heavy equipment present. We encounter them regularly on roadsides, yet few understand their full capabilities. What tasks do they perform? Why are they indispensable for various construction projects? How do they manage to excavate large holes so efficiently? What is their strength capacity?
This article delves into the functionalities of backhoes, explores the mechanisms enabling their operations, and demonstrates how operators control these machines. After reading, you'll have a clear understanding of what a backhoe loader is accomplishing the next time you see one in action by the freeway.
What is a Backhoe Loader?
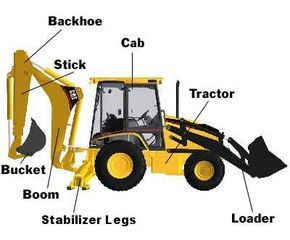
Backhoe loaders stand out with their distinctive design, featuring various protruding parts. While the purpose of a dump truck is immediately apparent, the functions of a backhoe's different attachments might not be as obvious.
The backhoe loader is a fascinating innovation, merging three types of construction machinery into one. It consists of:
- A tractor
- A loader
- A backhoe
Each component is designed for specific tasks. On most construction sites, operators utilize all three features of the backhoe loader to complete their work efficiently.
The Tractor
At the heart of a backhoe loader lies the tractor. Similar to agricultural tractors, this component is built to navigate challenging terrains effortlessly. It boasts a robust, turbocharged diesel engine, durable tires, and a cab equipped with essential controls like a steering wheel and brakes. Operators are shielded by either fully enclosed cabs or open canopy structures.
The Loader
Positioned at the front is the loader, while the backhoe is mounted at the rear. Each serves distinct purposes in construction tasks.
The loader is versatile, functioning akin to a massive dustpan or scoop. Primarily, it's employed for transporting hefty volumes of loose materials rather than digging. Additionally, it can level surfaces or push dirt, much like a plow. Operators manage the loader's functions while maneuvering the tractor.
The Backhoe
The backhoe serves as the primary tool of the backhoe loader, designed to excavate tough, compact materials like soil or to hoist heavy objects such as a sewer box. It can lift and deposit these materials into a pile beside the excavation site.
In essence, the backhoe functions as a massive, highly robust version of a human arm or finger. It consists of three main parts:
- The boom
- The stick
- The bucket
This structure closely resembles the human arm, which is divided into three segments: the upper arm, forearm, and hand.
The backhoe's segments are linked by three joints, similar to a human wrist, elbow, and shoulder. It operates much like an arm, with the boom on a Caterpillar® backhoe angled upward for easier digging around obstacles. This design also ensures ample room for the bucket when it's fully loaded and curled in.
The backhoe excels at digging various holes, particularly ditches. To operate it, the driver must park the tractor and swivel the seat to face the backhoe.
How do the tractor, loader, and backhoe work together? The tractor transports the loader and backhoe to different locations and is also used to maneuver the loader. The loader and backhoe complement each other perfectly for a range of tasks. After excavating dirt to create a ditch or hole, the loader is typically needed to remove the dirt or refill it once pipes, power lines, etc., are in place. A common task for a backhoe loader involves digging a trench with the backhoe and then back-filling it using the loader.
The Stabilizer Legs
Another notable feature of a backhoe loader is the pair of stabilizer legs located behind the rear wheels. These legs are vital for backhoe operations, as they absorb the majority of the weight during digging. Without them, the wheels and tires would bear the strain of heavy loads or the force of digging, causing the tractor to bounce. The stabilizers keep the tractor steady, reducing the impact of digging and preventing it from sliding into the ditch or hole.
The stabilizer legs feature two types of "shoes" to ensure stability on both dirt and pavement. The grouser shoe side grips dirt effectively but would damage roads. For asphalt, the operator switches to the rubber-padded shoe for a secure hold.
Why Are Backhoe Loaders So Popular?
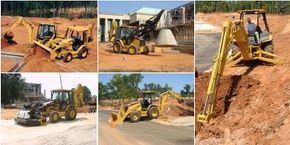
Backhoes have been in use for over 40 years and have grown in popularity over the past decade. Caterpillar alone has sold more than 100,000 units since 1985. Their widespread use stems from the fact that digging and moving dirt are essential to many projects, such as laying pipes, setting building foundations, and creating drainage systems. While other tools may perform these tasks more efficiently, backhoes remain a favorite due to their versatility and practicality.
One key advantage of backhoes is their compact size compared to larger, specialized machinery like excavators. They can navigate tight spaces and are road-transportable. Although mini-loaders and standalone backhoe units are smaller, combining both functions into one machine saves time by eliminating the need to switch between equipment.
The backhoe's popularity is also due to its impressive capacities. The Caterpillar backhoe loader shown above boasts immense power. Its backhoe can exert 15,200 pounds (67.6 kN) of digging force and extend over 25.9 feet (7.9 meters). The loader can lift up to 8,760 pounds (3,970 kg) and carry 1.75 cubic yards (1.3 cubic meters) of dirt in its standard bucket. While not as powerful as larger machinery, it handles even challenging tasks effectively.
Construction crews often prefer backhoes over more specialized equipment because of their versatility. For small to medium-sized digging tasks, a backhoe is more than adequate. Additionally, as we'll explore later, some backhoe models offer capabilities beyond just digging and loading.
Hydraulic Power
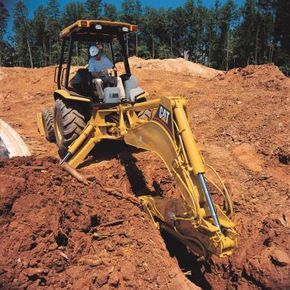
Watching a backhoe in action reveals its extraordinary power. A skilled operator can dig a 5-foot-deep, 10-foot-long ditch in under 15 minutes. Compare that to the time it would take using just a shovel! This efficiency is achieved through hydraulics, which use pressurized fluid to move pistons and generate force.
The idea of hydraulic machinery might seem strange—how can pumping liquid generate such power? However, the principle is straightforward. First, we'll explore the basics of hydraulic systems, and then we'll examine how backhoes utilize these systems to dig and move massive amounts of dirt.
Hydraulic systems transfer forces from one point to another using fluid. Most systems rely on an incompressible fluid, which is as dense as possible. This type of fluid transmits almost all the applied force without absorbing much of it. Oil is the most commonly used incompressible fluid in hydraulic machinery.
In a basic hydraulic machine, the operator applies force to the oil using one piston, causing the oil to push another piston, which then lifts.
Hydraulic multiplication
When the second piston has a larger diameter than the first, it moves a shorter distance but exerts a greater force.
The fundamental principle here involves a trade-off between distance and force. When you press down on the left piston, two factors come into play: the amount of force
Calculating the exact multiplication factor is straightforward. Suppose the left piston has a 2-inch diameter (1-inch radius), and the right piston has a 6-inch diameter (3-inch radius). The area of each piston is Pi * r. Thus, the left piston's area is 3.14 (3.14 * 1), while the right piston's area is 28.26 (3.14 x 3). The right piston is nine times larger, meaning any force applied to the left piston is multiplied nine times on the right. For example, a 100-pound downward force on the left piston creates a 900-pound upward force on the right piston. However, the left piston moves 9 inches, while the right piston rises only 1 inch, maintaining the force-distance balance.
In the backhoe loader shown above, the hydraulic system pumps oil at pressures up to 3,300 pounds per square inch, with cylinder pistons in the backhoe arm reaching diameters of 5.25 inches. This results in each cylinder piston exerting a force of 70,000 pounds!
Hydraulic Valves
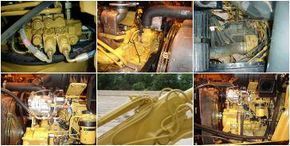
In our basic hydraulic machine, pressing down on oil with one piston caused a larger piston to rise, amplifying the applied force. This mechanism is ideal for systems requiring intermittent force, like a brake system. However, in equipment like a backhoe, pistons are constantly in motion, necessitating constant oil pressure.
In a backhoe, this pressure is generated by an oil pump driven by a diesel engine. The pump functions similarly to the narrow piston in our earlier example, applying a smaller force to the oil at high speed to create pressure that moves another piston more slowly but with greater force. The pump ensures a continuous flow of high-pressure oil to a valve block system, which directs the force (we'll explore this process in detail later).
The powerful pistons in a backhoe are driven by the same principles as the simple hydraulic system. However, there are key differences. The basic piston could only apply force in one direction—pushing down on the narrow piston caused the wider piston to rise. In contrast, a backhoe's arms must move in different directions to dig. This requires pistons that can both push and pull with full force, necessitating a more complex design.
If you were to examine a piston cylinder from a backhoe, it would look something like this:
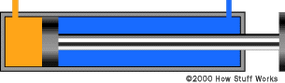
The piston rod extending outside the cylinder is driven by a piston head inside. Fluid on both sides of the piston head, supplied by two hoses, determines its movement. If the blue side has greater force, the piston moves left; if the orange side dominates, it moves right. Changing the direction of force simply involves redirecting oil flow. This type of piston cylinder is known as a hydraulic ram.
A backhoe loader employs a spool valve to direct oil to either side of a hydraulic ram, enabling the pistons to move in two directions.
The pump draws oil from a reservoir and sends it through a hose to the spool valve. When the operator adjusts the controls to change the backhoe's direction, the spool valve reconfigures, redirecting high-pressure oil to the opposite side of the ram. As high-pressure oil pushes one side, low-pressure oil is routed back to the reservoir through another hose.
The operator manages this valve block using joysticks in the backhoe cab. In some models, control sticks are directly connected to spool valves, functioning as levers to move the spool.
In other backhoes, the joysticks control hydraulic pistons that manipulate the spool valves. Moving the joystick in a specific direction presses a piston, which pushes oil through a hose to adjust the spool valve for a particular hydraulic ram. By shifting different spools, the operator extends or retracts various hydraulic pistons. In the following sections, we'll examine how these pistons are arranged and how their forces translate into the backhoe and loader's movements.
Hydraulics in the Backhoe
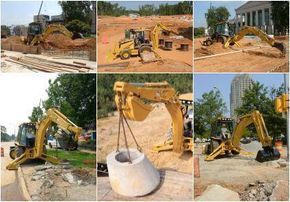
We've explored how the backhoe's valve system can move hydraulic pistons in two directions with immense force. But how do engineers utilize this technology to build such powerful digging machines?
Think of the backhoe as a massive, robust version of a human arm. We likened its steel segments—the boom, stick, and bucket—to the three parts of your arm, connected by joints. Just as your arm relies on muscles to move its segments, the cylinders in a backhoe perform the same role. These cylinders either pull connected segments closer or push them apart, enabling movement.
Each cylinder piston is managed by its own spool valve. When operating a backhoe, you control at least four spools, which move four pistons. The animation below demonstrates how an operator coordinates these pistons to dig effectively.
The backhoe also features two hydraulic pistons near the boom arm's base. The boom arm is attached to the tractor via a swing casting, allowing these pistons to swing the arm side to side. They work in sync—when one pushes, the other pulls. In many European backhoes, the boom is connected to a side-shift mechanism, enabling horizontal movement of the entire arm. This feature allows operators to dig in tight spaces where maneuvering the tractor would be challenging.
One of the most critical factors in backhoe performance is dig depth, which measures how deep the backhoe arm can excavate. Typically, this ranges between 12 and 16 feet (3 to 5 m). Many backhoes feature an extendable stick that can increase dig depth by a few feet when necessary. While most tasks don't require digging deeper than 10 feet, dig depth is still a valuable metric as it also indicates the backhoe's reach.
Another key specification is horsepower. If you're familiar with How Horsepower Works, you know it measures the amount of work an engine can perform over time. A backhoe's horsepower rating reflects the engine's power output, giving insight into the machine's overall capabilities.
Backhoes with greater dig depth often have higher horsepower. Enhancing both factors broadens the machine's functionality. Models designed for residential construction—such as digging foundations, grading, or laying sewer and utility lines—typically offer a dig depth of 14 to 16 feet and 70 to 85 horsepower. For heavier industrial and commercial tasks like road maintenance or large-scale construction, backhoes usually exceed 17 feet (5 m) in dig depth and provide at least 100 horsepower.
Backhoes are also rated by breakout force, which measures the maximum force the arm can exert on a load. This is determined by the bucket's pushing power, with all hydraulic rams contributing to the total force. Additionally, stick lift and boom lift ratings indicate the maximum weight the stick and boom can lift individually under full hydraulic force. These metrics are crucial for contractors using backhoes as makeshift cranes for heavy lifting. The backhoe pictured above boasts a 14,712-lb (65.4-kN) breakout force, a 6,250-lb (2,830-kg) stick lift capacity, and a 3,940-lb (1,787-kg) boom lift capacity.
Hydraulics in the Loader
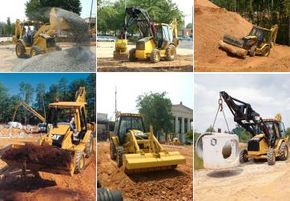
While we've primarily discussed the backhoe, the loader also operates using hydraulics. Its hydraulic rams are arranged in pairs, functioning similarly to how you would lift a heavy box—using both arms simultaneously. The valve system ensures equal oil flow to each ram in the pair, allowing them to move in sync and stabilize the loader bucket.
Caterpillar offers two loader types for its backhoes: a single tilt (yellow) and a parallel lift (black). Both use a pair of pistons to raise and lower the loader arms, which are connected to the tractor and the bucket. Parallel-lift loaders feature a second pair of rams attached to the bucket, enabling it to tilt and dump. Single-tilt loaders achieve this with a single central ram.
Parallel-lift loaders utilize an eight-bar-linkage design, enhancing loading efficiency. This system keeps the bucket level as it rises, preventing material from spilling. Without parallel lift, the loader would operate like a seesaw, causing contents to fall out when tilted. The parallel-lift mechanism ensures smoother and more effective loading by maintaining the bucket's alignment with the ground.
Some backhoe loaders feature ride control, a technology that improves ride smoothness. Carrying a full load can be bumpy due to the small wheelbase relative to the equipment's inertia. Ride control uses the loader's hydraulic system as a shock absorber. As the bucket bounces, it compresses oil in the hydraulic cylinders, which flows into an accumulator containing compressed nitrogen gas. The gas acts like a spring, absorbing shocks and stabilizing the ride.
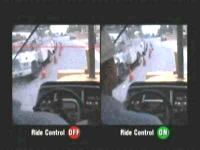
Without a damping mechanism, the oil would oscillate, causing the bucket to bounce continuously. To smooth the ride, the ride control system absorbs energy as oil flows. This is achieved through a damping mechanism—a small orifice in the hose connecting the lift ram to the ride control accumulator. As the loader bucket bounces, oil is forced through this narrow opening, converting the energy into heat. This energy loss dampens the bouncing, resulting in a more stable ride.
Similar to backhoe arms, loaders are rated by their breakout force. This rating indicates the maximum force the loader's hydraulic rams can exert on the front bucket, providing insight into its pushing and lifting capabilities.
Operating the Backhoe Loader
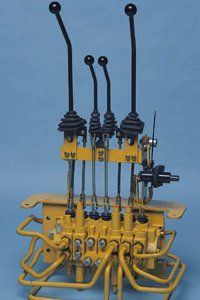
Considering the numerous moving parts in a backhoe loader, it’s astonishing that only one person operates it. As we’ve seen, the backhoe arm pivots on four hinges (sometimes five), the loader moves on two to three hinges, and the operator manages the stabilizer arms and tractor movement simultaneously. How does one person handle all this?
A Caterpillar backhoe is controlled using two joysticks, similar to computer controls. Here’s how they function:
- The joystick on the left controls the boom and swings the backhoe side to side.
- The right joystick operates the stick and bucket.
- Pulling a joystick toward you brings the boom or stick closer, while pushing it away extends them outward.
- Moving the left joystick left or right swings the backhoe arm in that direction.
- Moving the right joystick left scoops the bucket, while moving it right dumps the bucket.
Mastering backhoe operation takes practice, much like learning to drive. The challenge lies in coordinating multiple actions simultaneously. Just as driving requires awareness of various controls, operating a backhoe demands the same focus. Moving your arm naturally is effortless, but imagine having to consciously control every muscle involved in a single motion—this is the complexity of backhoe operation.
Experienced drivers perform most actions instinctively, and backhoe operators achieve the same level of proficiency. With practice, the controls become automatic. Beyond mastering the controls, operators must also learn to position the arm for efficient digging. This includes understanding the optimal bucket angle, when to adjust the boom or stick, and which arm positions offer the best leverage.
Operating the loader is straightforward, as it only performs three actions: dumping, raising, and lowering. The primary control is a joystick on the operator's right side. Pulling the joystick toward you lifts the arms via the hydraulic rams, while pushing it away lowers them. Moving the joystick to the right dumps the bucket, and moving it to the left scoops it in.
The loader is simpler to master compared to the backhoe. However, to use it effectively, operators must maneuver the tractor simultaneously. The tractor operates like a car, with a steering wheel, accelerator, brake pedal, and gear shift. Both the loader and tractor are powered by the same engine, which has variable speed control. For an extra boost in loader power, the operator can shift the tractor into neutral, directing most of the engine's power to the hydraulic system.
Skilled backhoe operators use the machine much like you would use a shovel or wheelbarrow at home—they know precisely how to manipulate the controls for efficient digging and loading. They also plan ahead, anticipating their next moves, similar to how a driver navigates traffic. Learning to operate the backhoe is just the beginning; true expertise lies in using it effectively for various tasks.
Click here to see a 360-degree view from the operator's cab.
The Hydraulic Pump
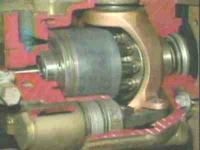
The hydraulic pressure for all systems in a backhoe comes from a hydraulic pump. There are two commonly used types of pumps:
- Gear pumps
- Variable-displacement pumps
A gear pump uses interlocking gears to pressurize hydraulic oil. However, its pressure fluctuates with engine speed, requiring full engine power to achieve high pressure.
A variable-displacement pump is more advanced. It features piston cylinders arranged in a ring within a rotating barrel. The pistons extend to an angled swash plate, which pushes and pulls them as the barrel spins. This action draws oil from the tank and pumps it into the hydraulic system. The swash plate ensures maximum oil intake and discharge, pressurizing the oil for powerful output.
The core of the load-sensing hydraulic system is the variable-displacement pump.
This pump is particularly impressive because its oil output can be easily adjusted by changing the angle of the swash plate. When the swash plate is closer to the barrel, the difference in cylinder fluid compartment sizes is minimized, reducing oil flow. If the swash plate is flat against the barrel, the system stops pumping oil entirely.
The swash plate's angle is controlled by the hydraulic system's demands. Special circuits monitor hydraulic ram pressure and adjust oil flow accordingly. This load-sensing system offers significant advantages over fixed-displacement pumps.
First, the variable-displacement pump is more efficient, as it only pumps the oil required by the system. When no hydraulic rams are active, the pump stops, significantly reducing fuel consumption.
Second, this system optimizes engine power usage. Most backhoes have multiple engine-speed settings. At maximum speed, the backhoe operates with peak power, while reduced speeds limit available power.
If the pump attempts to use more power than the engine can deliver at a given speed, the engine will stall. To ensure maximum hydraulic pressure at all times, the system must intelligently manage the available power.
In a backhoe, power is calculated by multiplying flow rate by hydraulic pressure. The pressure depends on the task—lifting heavy loads or breaking through tough ground requires higher pressure than moving an empty bucket. Relief valves set the hydraulic system's maximum pressure.
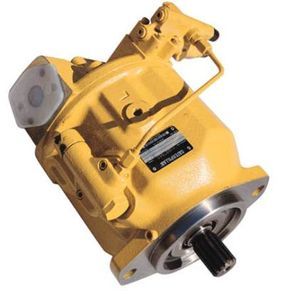
Backhoes with fixed-displacement pumps maintain a constant flow rate at any engine speed. Since flow rate multiplied by maximum pressure cannot exceed engine power, the system always pumps oil at the rate needed for maximum pressure. Some oil is used by the hydraulics, while the rest returns to the tank. This results in wasted engine power and unnecessary wear if full pressure isn't required.
Backhoes with variable-displacement pumps avoid this issue. The system monitors hydraulic ram pressures and adjusts the swash plate angle to meet the highest pressure demand. If full pressure isn't needed, the pump increases displacement (and flow rate) to speed up tool movement. When full pressure is required, the pump reduces displacement to stay within the engine's power limits.
Attaching Different Tools
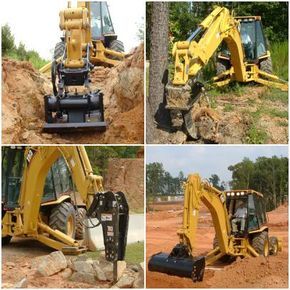
Certain backhoe-loaders allow you to attach a range of tools to the backhoe stick or loader, replacing the standard buckets. Caterpillar models feature an integrated toolcarrier (IT) that simplifies the connection of compatible attachments. These tools include specialized buckets, street sweepers, and pallet forks.
The backhoe arm also facilitates easy attachment of various tools. As shown in the video below, the operator secures the tool to the backhoe stick using a connecting pin. Available tools include:
- Hydraulic hammers for breaking asphalt
- Augers for drilling circular holes
- Asphalt grinders for road surface milling
- Grapples for gripping and removing rooted materials like tree stumps
The capability to attach various tools significantly enhances the backhoe's versatility. These attachments enable the backhoe loader to perform a wide range of tasks on the job site.
Inside a Backhoe Loader
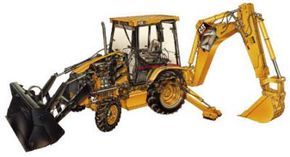
As we've seen, backhoe loaders are packed with hydraulic valves and cylinders. They also include components common to tractors, cars, and trucks. In this section, we'll explore some of the essential parts that make a backhoe function.
Every backhoe loader comes equipped with a set of standard components. These include:
- An engine - In most backhoe loaders, the tractor, loader, and backhoe are powered by a diesel engine. The Caterpillar 80-horsepower 3054 engine features a 4-cylinder, 4-stroke, direct-injection design. It includes a dry-type, radial-seal two-stage air filter and a thermal starting aid for reliable starts even at -20 degrees Fahrenheit (-29 C). While the base model is naturally aspirated, some Caterpillar backhoes come with a turbocharged option. For more on engines, explore How Engines Work, How Diesel Engines Work, and How Turbochargers Work. Photo courtesy Caterpillar The diesel engine from a Caterpillar backhoe
- A transmission - To transfer engine power to the tractor and hydraulic systems, a transmission is essential. Similar to a car's transmission, it allows gear shifting, forward and reverse movement, and efficient power use. Backhoe loaders offer either automatic or manual transmissions. The Caterpillar power-shuttle transmission provides four speeds and forward/reverse functionality. It features hydraulically shifted shuttle clutches for on-the-go direction and speed changes, along with a torque converter for optimal power efficiency. Learn more in How Manual Transmissions Work, How Automatic Transmissions Work, and other articles in the transmission category. Photo courtesy Caterpillar The transmission from a Caterpillar backhoe
- Axles - The wheels are driven by axles. The Caterpillar standard rear axle has an enclosed design, protecting it from harsh conditions and ensuring reliable operation. Photo courtesy Caterpillar A standard rear axle from a Caterpillar backhoe
- Brakes - Like cars, backhoe loaders require brakes to stop. Caterpillar models use hydraulically-actuated, self-adjusting disc brakes for stopping and a separate parking brake operated by a hand lever. For more on brakes, see How Brakes Work. Graphic courtesy Caterpillar A close-up of the rear brake from a Caterpillar backhoe
These components, along with all other backhoe parts discussed, are mounted on a durable steel frame.